Welcome to our comprehensive guide on concrete prices per cubic meter (m3) in New Zealand, designed to help you make informed choices for your next project. Whether you’re planning a home renovation, laying down a new driveway, or tackling a larger commercial build, understanding the cost factors that affect concrete pricing is crucial for accurate budgeting and achieving long-lasting results. In this guide, we’ll break down the essentials of concrete costs, including the types of concrete available, factors that impact price variations, and practical tips to help you save on expenses while ensuring high-quality, reliable results for your construction needs.
On average, the price of concrete per cubic meter (m3) in New Zealand ranges from NZD 150 to $250, depending on factors like concrete type, strength (MPa rating), and delivery location. Specialty mixes and higher-strength concrete can increase the price, while bulk orders may offer some cost savings.
- Why Knowing The Price Of Concrete Per m3 Matters
- Overview Of Concrete Use In New Zealand
- Factors Affecting Concrete Price Per m3 In NZ
- Typical Concrete Price Range Per m3 In New Zealand
- Tips For Saving On Concrete Costs
- Understanding Concrete Quality And Durability
- Common Questions About Concrete Pricing In New Zealand
- Final Tips For Budgeting And Planning Your Concrete Project
- FAQs: About Concrete Price Per M³ NZ
- Conclusion
Why Knowing The Price Of Concrete Per m3 Matters
Understanding the cost of concrete per cubic meter (m³) is crucial for any construction project, big or small. Whether you’re managing a residential build, a commercial project, or a major infrastructure initiative, knowing how much concrete costs is essential for budgeting, planning, and achieving a successful outcome. Below, we’ll explore why concrete pricing holds such significance, from its financial implications to its environmental and structural impact.
Accurate Budgeting for Concrete-Heavy Projects
Concrete is a foundational material in construction, forming the backbone of various structures like foundations, walls, and pavements. With concrete used so extensively, its cost can significantly affect your project’s budget. When you know the price per cubic meter of concrete, you gain a clearer view of what to expect financially. Without this knowledge, budgeting can be a guessing game, which can lead to unplanned expenses that snowball into major financial setbacks.
For instance, if you’re pouring a driveway or setting a foundation, you’ll need to calculate how much concrete is required, which is directly influenced by both the dimensions of the area and the thickness of the concrete slab. Even a small discrepancy in pricing can multiply over larger areas, making it imperative to get precise cost estimates per m³.
Concrete Costs and Overall Project Budgets
The cost of concrete doesn’t just affect the raw material expenses; it impacts the overall budget because concrete-related expenses often extend beyond the concrete itself. Labor, transportation, and preparation work are all tied to the amount and type of concrete needed, which means misjudging concrete prices could leave you paying significantly more than anticipated.
For projects with strict budgets, these additional costs can put a serious strain on financial resources. By knowing concrete costs upfront, project managers and homeowners can allocate their funds more effectively, ensuring that essential project elements are covered without unexpected financial hiccups. This transparency fosters better planning, prevents delays, and reduces the chances of needing to source additional funding mid-project.
Environmental and Structural Significance of Concrete Quality
Concrete is not just any material it’s an engineered product that comes in different types, each tailored to meet specific structural needs. Choosing the right concrete type can directly influence both the durability and safety of your structure. For example, high-strength concrete is essential for heavy-load-bearing structures like bridges or high-rise buildings, whereas lightweight concrete might be preferred in residential applications where less load is expected.
However, the choice of concrete also has environmental considerations. Different types of concrete require different amounts of cement, water, and aggregates, each carrying its own environmental footprint. High-quality concrete may come at a premium but often results in less waste, longer-lasting structures, and potentially lower long-term maintenance costs. By understanding the price per m³, you can make an informed decision that balances cost-effectiveness, structural integrity, and environmental responsibility.
In summary, knowing the cost of concrete per cubic meter offers a valuable perspective that informs budgeting, ensures the stability and longevity of structures, and supports sustainable building practices. Whether for a DIY project or a major construction endeavor, understanding this cost is a cornerstone of effective planning and project success.
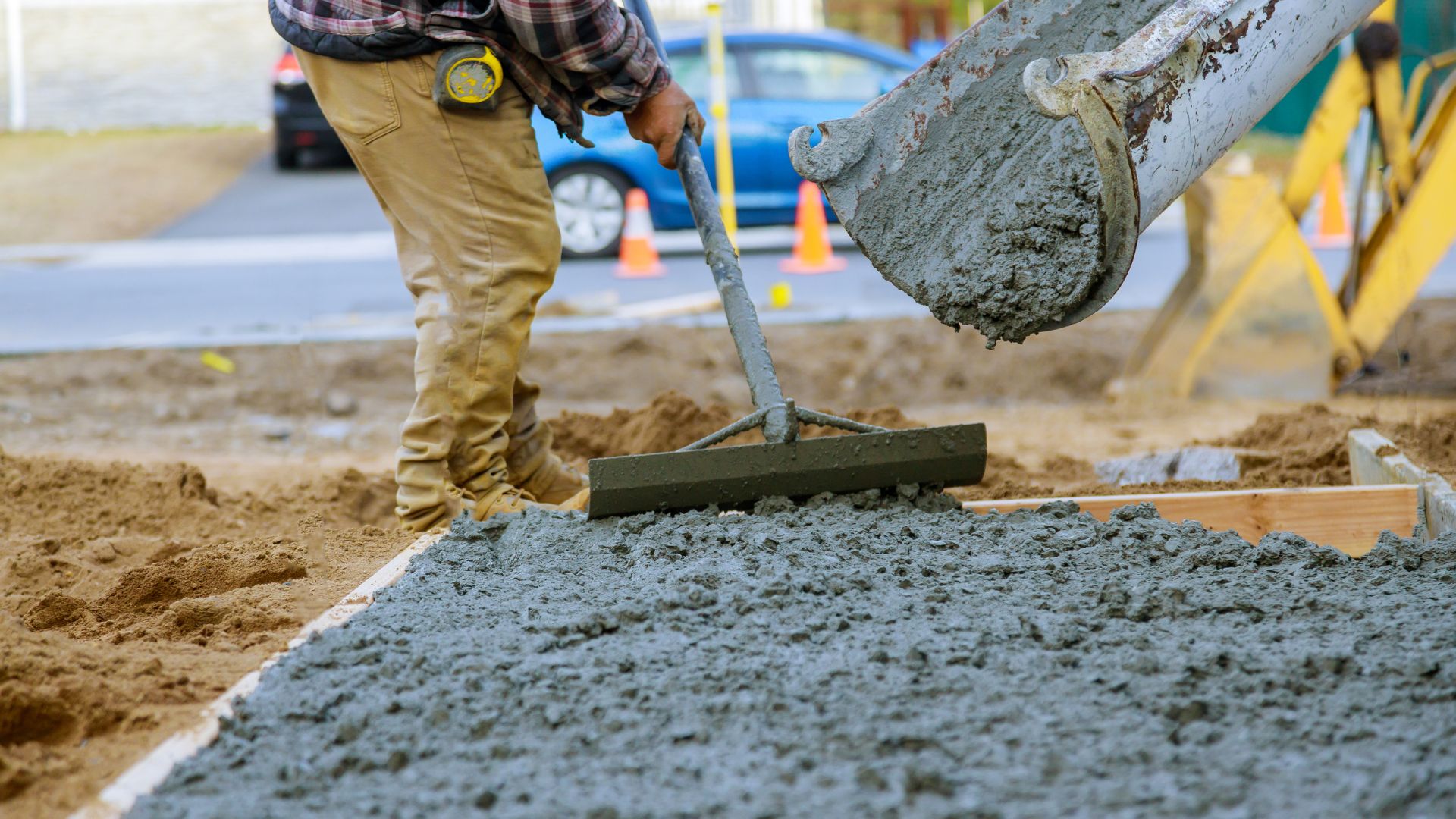
Overview Of Concrete Use In New Zealand
Concrete is a cornerstone of construction across New Zealand, playing an essential role in building resilient structures, both big and small, for residential, commercial, and public purposes. With its reputation for strength, durability, and versatility, concrete is widely used for a range of applications that extend from single-family homes to complex infrastructure. Here, we dive into the popular uses of concrete, the types of projects it is commonly used for, and how demand is growing across different sectors throughout the country.
Popular Applications of Concrete in Residential and Commercial Construction
In both residential and commercial construction, concrete stands out as one of the most reliable building materials, appreciated for its robustness, flexibility, and longevity. For residential projects, concrete is commonly used to create foundations, driveways, patios, and even outdoor features like pathways and retaining walls. Homeowners and developers alike turn to concrete due to its cost-effectiveness and resilience against New Zealand’s varying climate conditions, from coastal regions to inland areas.
Commercial buildings, such as office complexes, shopping centers, and warehouses, also frequently rely on concrete for foundational support, flooring, and structural components. Given the high foot traffic and daily operational loads in commercial environments, concrete is an ideal material, ensuring the longevity and stability of these buildings. Its use isn’t limited to floors or walls; concrete is often molded into custom shapes and finishes, providing aesthetic appeal without compromising functionality.
Common Types of Concrete Projects in New Zealand
Concrete has become integral to numerous project types in New Zealand, adapting to various functional and aesthetic demands across construction. Some of the most common types of concrete projects in New Zealand include:
- Foundations: Concrete foundations form the backbone of residential and commercial properties alike, ensuring structural stability and safety. Given New Zealand’s geological variability, concrete foundations are often reinforced to withstand seismic activity, a critical feature in earthquake-prone regions.
- Driveways and Pathways: Concrete driveways and pathways are popular choices for both homeowners and commercial properties. Known for their durability and low maintenance, concrete surfaces handle heavy traffic and are resistant to weathering, ideal for New Zealand’s diverse climates.
- Patios and Outdoor Living Spaces: Concrete patios have surged in popularity as Kiwis embrace outdoor living. Concrete’s versatility allows for customization in colors, textures, and finishes, creating inviting outdoor spaces that are both stylish and functional.
- Retaining Walls: In hilly or sloped terrains, retaining walls are essential for preventing soil erosion and managing landscape elevations. Concrete retaining walls are not only effective but also visually appealing, integrating seamlessly into residential gardens, parks, and public spaces.
Increasing Demand for Concrete in Housing, Infrastructure, and Landscaping
New Zealand’s construction sector has experienced a noticeable increase in demand for concrete, largely driven by rapid urbanization, population growth, and an ever-increasing need for resilient infrastructure. The housing market, in particular, has witnessed a significant boost, as concrete has become a preferred choice for developers aiming to create homes that withstand the test of time and offer low maintenance. Concrete’s eco-friendly potential, especially with newer sustainable mixes, appeals to developers focused on reducing environmental impacts.
In infrastructure, concrete plays a key role in projects such as roads, bridges, tunnels, and water treatment facilities. These public projects require durable, long-lasting materials to ensure public safety and reduce the frequency of repairs, minimizing disruptions to daily life. This makes concrete invaluable for government and private sectors alike as they invest in infrastructure improvements across New Zealand.
Lastly, concrete’s demand in landscaping has grown substantially, as architects and homeowners seek materials that blend well with natural landscapes while offering enduring performance. From garden walls to custom seating and decorative pathways, concrete’s versatility and range of finishes enable it to complement diverse landscaping designs, helping homeowners and landscapers alike enhance outdoor aesthetics without sacrificing durability.
In summary, concrete’s role in New Zealand’s construction landscape is undeniable, with its popularity stretching across residential, commercial, and public sectors. From foundations to driveways, and patios to retaining walls, the range of projects relying on concrete reflects its adaptability and strength. As demand continues to grow, concrete remains a preferred building material, promising enduring structures that are as resilient as they are sustainable and suitable for New Zealand’s unique environmental and architectural needs.
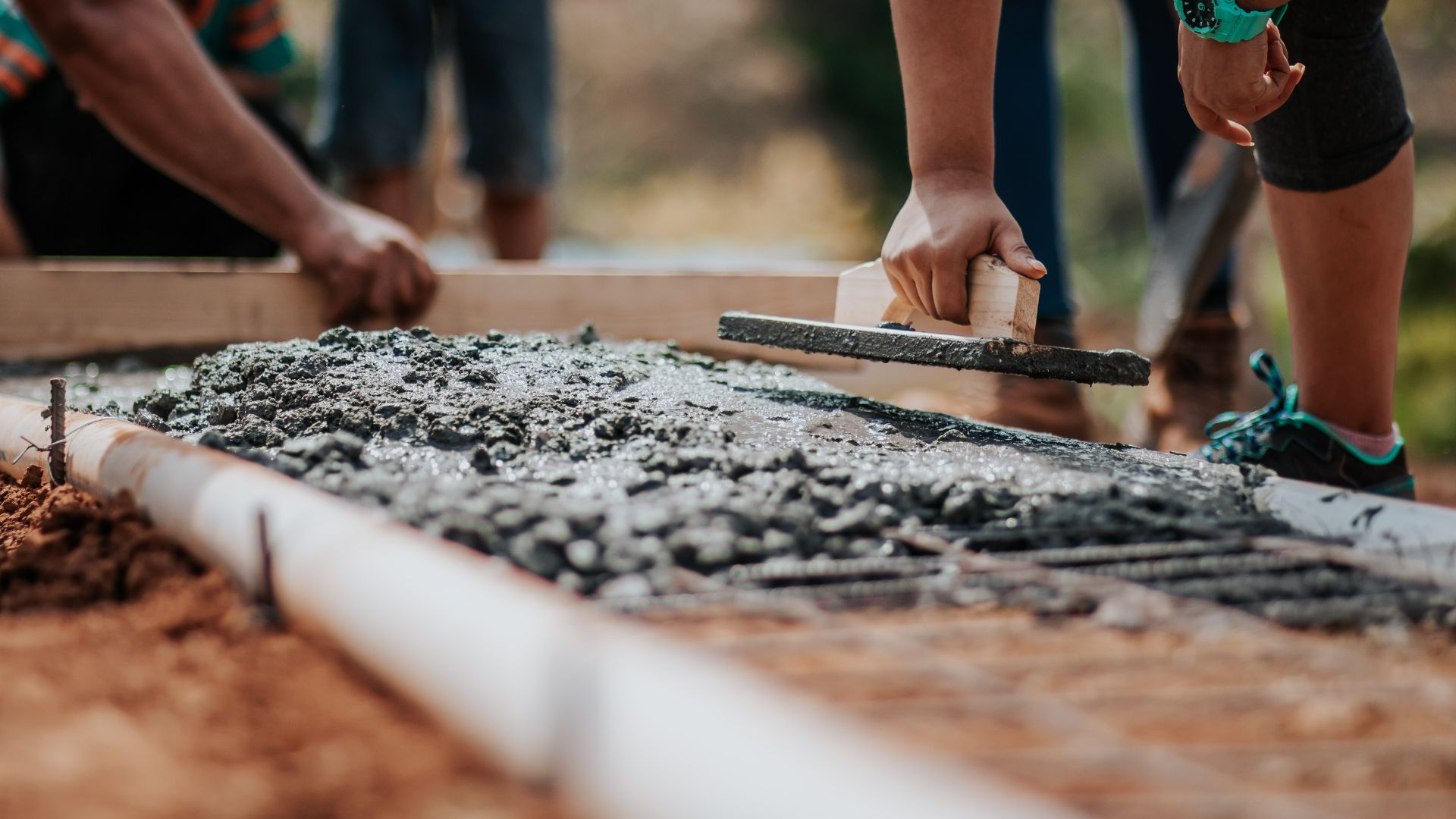
Factors Affecting Concrete Price Per m3 In NZ
When planning a construction project, understanding what influences the price of concrete per cubic meter (m3) in New Zealand can help you make better choices. Concrete pricing depends on a range of factors, from the type of concrete you select to the timing of your order. Here’s a closer look at what drives concrete costs and how to choose the best options for your budget and project. For current market rates, check with local suppliers such as Allied Concrete a reputable source for concrete across New Zealand.
Type of Concrete
Concrete isn’t a one-size-fits-all material. The mix you choose can significantly impact the price due to varying ingredient ratios, strength requirements, and finishing touches. Here’s a quick breakdown of common types:
- Standard Concrete: This mix is widely used for general construction purposes, like driveways and floors. It’s relatively affordable and versatile, making it a go-to for many projects.
- High-Strength Concrete: If your project demands durability and load-bearing capacity, high-strength concrete is ideal but comes with a higher price tag. This is often used in commercial or industrial applications.
- Decorative Concrete: Decorative options, such as colored or stamped concrete, are popular for patios and feature walls, offering aesthetic appeal but typically at a premium due to extra additives and specialized application methods.
Additionally, specialized concrete like ready-mix, pre-mixed, and fiber-reinforced types offer added convenience, strength, or crack resistance. While beneficial for specific needs, they tend to cost more due to the technology and materials used in production.
Concrete Strength (MPa Rating)
The MPa (Megapascal) rating measures the concrete’s strength, essentially indicating how much load it can handle. Higher MPa ratings mean greater strength and durability, often needed for commercial projects or structures subject to heavy use.
- Typical MPa Ratings in New Zealand: Most residential projects use concrete with an MPa rating between 20 to 25, while commercial applications may range from 30 MPa and up. Higher ratings generally translate to increased cost per cubic meter, as they require a more robust mix of cement and aggregate.
The cost difference between, say, 20 MPa and 40 MPa concrete can be substantial. However, investing in the appropriate strength for your project is crucial, as it ensures longevity and structural integrity.
Location and Delivery Costs
The location of your site relative to the concrete supplier can heavily influence final pricing. Transporting concrete requires specialized vehicles, often with limited travel time due to the material’s setting properties.
- Urban vs. Remote Deliveries: Concrete suppliers in cities or well-connected areas generally offer more competitive rates than those servicing rural locations, where transportation may be complex or time-intensive. In remote regions, expect additional fees to cover the logistical challenges and extra time needed to reach the site.
- Additional Delivery Charges: In some cases, projects in hard-to-access areas (e.g., rugged terrains or construction zones) may incur surcharges. Consider discussing these details with your supplier beforehand to avoid unexpected costs.
Quantity Ordered
Concrete is often more affordable per cubic meter when ordered in larger quantities. For instance, buying in bulk for a large project can reduce the price per m3 because suppliers save on transportation and production costs.
- Order Size and Pricing: Small orders (typically below 3-4 m3) can lead to higher costs per unit due to the supplier’s effort in mixing and delivering smaller quantities. For smaller residential projects, consider consolidating orders where possible to benefit from a lower unit rate.
- Bulk Ordering Advantages: Larger projects, such as commercial builds or extended residential additions, can benefit significantly from bulk ordering. Bulk rates not only reduce costs but also streamline the delivery process, keeping your project on schedule.
Seasonal Demand and Supplier Pricing
The time of year you order concrete can influence prices due to seasonal demand. In warmer months, demand tends to rise as construction activity increases. Higher demand can result in slightly higher prices per m3, as suppliers work to meet increased orders.
- Seasonal Trends in New Zealand: During the peak construction season, suppliers may have a longer lead time or introduce surge pricing. Additionally, global supply chain challenges, as seen recently, may impact material availability and pricing, making it wise to book your concrete early if possible.
- Market Fluctuations: Current economic conditions can also affect concrete prices, as raw material costs fluctuate. Staying informed about market trends can help you plan purchases effectively and lock in favorable rates.
Making Informed Decisions on Concrete Costs
Being aware of the factors that affect concrete pricing in New Zealand allows you to make smarter purchasing choices and manage your construction budget effectively.
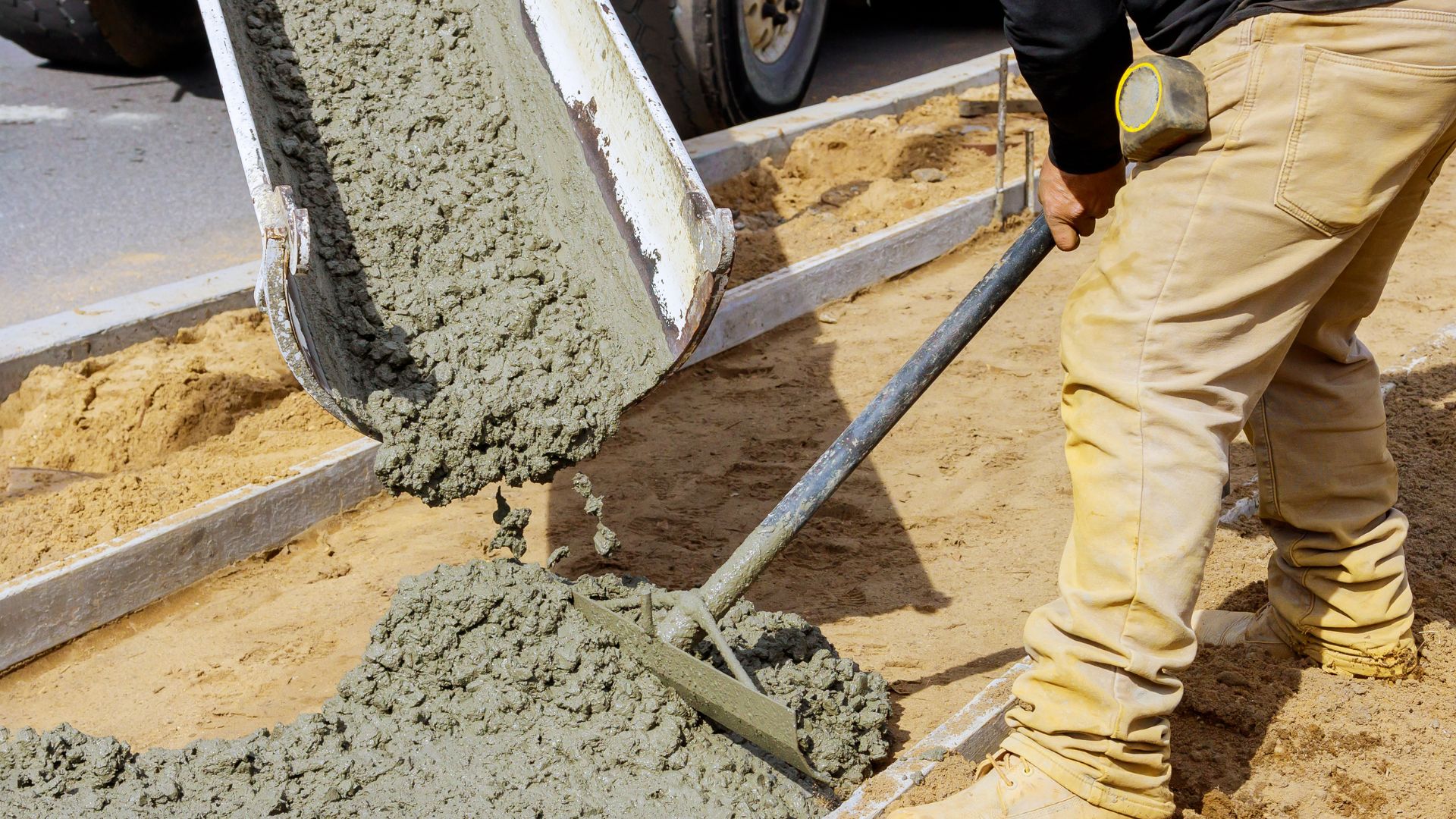
Typical Concrete Price Range Per m3 In New Zealand
Understanding the cost of concrete is crucial for anyone planning a construction project, whether it’s a simple driveway, a commercial building foundation, or a decorative patio. The price of concrete in New Zealand varies significantly depending on the type of mix, the project requirements, and additional factors like location and time of delivery. In this section, we’ll provide a general price range and highlight the different types of concrete mixes available. We’ll also explore any potential extra charges that may affect the overall price per cubic meter (m³), helping you budget effectively.
Concrete Price Range in New Zealand for Basic Mixes
For standard concrete projects, like driveways, flooring, and general building foundations, the cost for a basic concrete mix typically falls between NZD 160 to $200 per m³. Basic mixes are formulated to meet the standard strength requirements for everyday applications, making them a common choice for residential and light commercial projects. However, the final price will depend on the specific requirements of your project, such as the thickness of the pour, reinforcement needs, and proximity to the supplier.
Key Takeaways for Basic Mix Prices
- Application Suitability: Best for standard applications like foundations, driveways, and floors.
- General Cost Range: Expect to pay between NZD 160 to $200 per m³.
- Factors Influencing Price: Proximity to suppliers, bulk order discounts, and potential customization can slightly adjust this range.
High-strength or Specialty Concrete Mixes
High-strength or specialty concrete mixes, often required for projects with higher load-bearing needs, such as multi-story buildings or industrial applications, come at a premium. The added strength and specialized formulations for such concrete increase production costs. In New Zealand, prices for these high-strength mixes typically range from NZD 220 to $270 per m³.
Some common specialty mixes include:
- High-strength concrete: Ideal for structural components requiring greater durability.
- Lightweight concrete: Often used in structures where reducing load is essential, like upper-story flooring.
- Rapid-setting concrete: Great for projects with tight timelines, as it significantly reduces curing time.
Considerations for Specialty Mixes
- Higher Cost: Specialty and high-strength mixes are generally more expensive, with prices ranging from NZD 220 to $270 per m³.
- Best Applications: Recommended for projects with specific structural or durability requirements, such as multi-story buildings, foundations for heavy machinery, or areas with extreme exposure to elements.
- Increased Preparation Needs: These mixes may also involve more precise planning and may require professional oversight during the pour.
Decorative or Colored Concrete Options
Decorative or colored concrete is increasingly popular for residential and commercial projects where aesthetics are essential. Options like stamped, colored, or polished concrete offer unique visual appeal, turning ordinary surfaces into attractive features. The price of decorative concrete typically ranges from NZD 180 to $300 per m³, depending on the complexity and type of finish.
Popular decorative concrete types include:
- Colored Concrete: Additives provide a unique color palette for vibrant patios, pathways, and driveways.
- Stamped Concrete: Mimics natural materials like stone or brick, commonly used for patios, walkways, and outdoor entertaining areas.
- Exposed Aggregate: Offers a textured finish with visible stones, ideal for driveways or pool surrounds.
Key Points for Decorative Options
- Higher Costs Reflect Customization: Expect to pay more for decorative concrete due to extra labor and materials involved in achieving the desired appearance.
- Enhanced Curb Appeal: Decorative options elevate the aesthetic value of any project, often adding long-term value to properties.
- Wide Price Range: Prices can range from $180 for simple colored concrete to NZD 300 per m³ for complex decorative treatments.
Additional fees for Concrete Delivery
In addition to the cost of the concrete itself, be aware that most suppliers add fees for delivery and other specific services. These charges can vary but typically include:
- Delivery Fees: Standard delivery fees apply for most orders, usually based on distance from the supplier. Expect higher fees if you’re in a remote area.
- After-Hours Surcharge: Projects requiring weekend, late-night, or early-morning delivery often incur additional fees due to increased operational costs.
- Small Load Fees: If your project requires less than a full truckload, many suppliers add a surcharge to offset the logistical costs.
Estimating Total Costs
- Project Timeline: If your project requires rapid completion, consider potential after-hours charges.
- Batch Size: Ordering in bulk often lowers the per m³ price and may reduce or eliminate small load fees.
- Accessibility: For projects in hard-to-reach areas, additional handling fees might apply.
While these prices provide a reliable estimate, it’s essential to contact local suppliers for specific quotes based on your project’s unique requirements. Prices can vary widely due to market fluctuations, regional differences, and specific project needs. Preparing a well-rounded budget with the information above will help ensure a smooth process, from ordering your concrete to final project completion.
Consider all aspects type of mix, additional fees, and potential surcharges to get an accurate idea of total concrete costs in New Zealand.
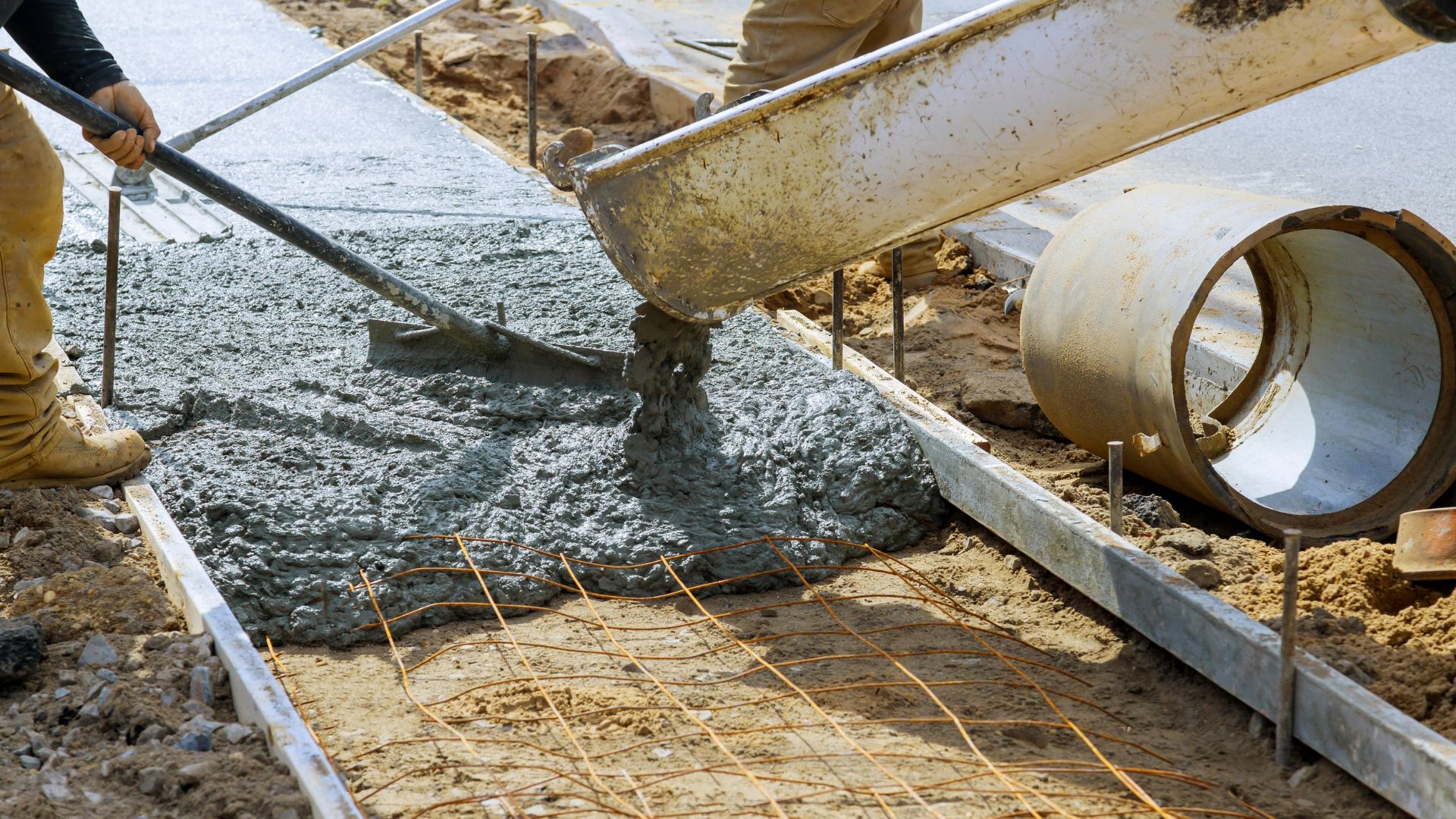
Tips For Saving On Concrete Costs
Concrete can be a major expense in construction, but with the right strategies, you can significantly cut down costs without sacrificing quality. Whether you’re building a driveway, foundation, or large-scale project, these practical tips can help you stay within budget. From ordering the right amount to smartly timing your project, here’s a detailed breakdown of how to maximize your savings.
Order the Right Quantity
Ensuring you purchase the correct amount of concrete is essential to avoid unnecessary costs. Ordering too much will leave you with wasted materials while ordering too little could lead to costly delays as you wait for more concrete to be delivered. Here’s how to calculate accurately:
- Measure Carefully: Start by measuring the area’s length, width, and depth to determine the total volume of concrete required. Online calculators are helpful for quick estimates, but remember that different projects require different thicknesses.
- Account for Waste and Overfill: Add 5-10% extra to account for waste. This margin will cover minor miscalculations or the need to overfill slightly to ensure a smooth finish.
- Consult Professionals if Needed: For complex jobs, consulting a contractor or a concrete professional can ensure accuracy, preventing costly errors in your estimates.
Compare Quotes from Local Suppliers
Concrete prices vary significantly between suppliers, so shopping around is vital. Even a small price difference per cubic yard can add up when ordering in bulk. Here’s how to get the best value:
- Request Detailed Quotes: Ask for an itemized breakdown from each supplier, including base price, delivery fees, and any additional charges for distance or weekend delivery.
- Compare Delivery Surcharges: Some suppliers add fuel or distance-based surcharges, especially if you’re located far from their facility. Check if nearby suppliers offer lower delivery fees.
- Negotiate Where Possible: For larger orders, there may be room for negotiation. Small discounts or waivers on delivery fees can make a big difference in total cost.
Consider Alternatives or Additives
Concrete comes with many customization options that can impact cost. By choosing recycled concrete or using specific additives, you can cut expenses while still achieving durable, high-quality results.
- Recycled Concrete: Using recycled concrete aggregate is a sustainable and cost-effective option for many projects. It’s particularly useful for applications where ultra-smooth finishes aren’t essential.
- Additives Like Fly Ash or Slag: Additives such as fly ash, slag, or silica fume can replace a portion of the cement in concrete mixes, reducing overall material costs. These additives can also enhance concrete’s strength and durability, making them a win-win for your project.
- Consult on Compatibility: Discuss with your supplier or contractor which alternatives work best for your project to ensure compatibility with your design requirements.
Plan Your Project During Off-Peak Times
Concrete suppliers experience fluctuations in demand based on the season, day of the week, and even the time of day. Timing your project strategically can mean big savings.
- Avoid Peak Seasons: Busy seasons, especially late spring through early fall, are when concrete suppliers are most in demand. If possible, plan your project in late fall or winter to take advantage of lower prices.
- Schedule for Weekdays or Off-Hours: Many suppliers charge a premium for weekend or after-hours deliveries. Opting for a weekday delivery can help you avoid these surcharges.
- Monitor Supplier Schedules: If your project timeline allows, ask suppliers when their downtime typically occurs and schedule accordingly. They may offer you a reduced rate if they can deliver during their less busy periods.
Reduce Labor Costs
Labor is a significant part of any concrete project’s expense, but there are ways to optimize it without compromising quality.
- DIY Small Jobs: For minor projects like garden paths, small slabs, or other manageable areas, consider tackling the work yourself. Many DIY resources can guide you through the process step-by-step, saving you on labor costs.
- Hire Skilled Laborers Efficiently: If your project requires professionals, choose laborers with specific experience in concrete. Experienced workers will work more efficiently, reducing the time (and cost) needed for the job.
- Avoid Unnecessary Overtime: Ensure that your project is well-organized, with materials and tools ready, to avoid paying for extended labor hours.
By following these strategies, you can make smart decisions that lower your overall project costs while ensuring a high-quality concrete installation. Whether you’re tackling the job yourself or hiring professionals, planning and efficiency are key to maximizing your savings.

Understanding Concrete Quality And Durability
In construction, one of the most critical considerations is concrete quality and durability. Achieving a balance between cost and quality is essential, especially when aiming to create safe, long-lasting structures. When planning construction projects, quality concrete is not an area to compromise because it directly impacts the lifespan and resilience of a building. Let’s break down why concrete quality is fundamental to durability, particularly in challenging environments like New Zealand’s, and explore how investing in high-quality concrete can yield significant long-term savings.
Balancing Cost and Quality for Strong, Durable Structures
Building with durable materials is critical for both safety and longevity, especially when it comes to concrete, which forms the backbone of most construction projects. Concrete quality is a direct factor in the structural integrity and resilience of buildings. While it may be tempting to cut corners to reduce costs initially, low-quality concrete can lead to expensive problems down the line. Compromising concrete quality might seem like a cost-saving decision in the short term, but the reality is that poor-quality concrete may not stand up well to environmental stressors, increasing the likelihood of costly repairs or even early structural failure.
High-quality concrete, on the other hand, offers stability and strength that can withstand various conditions, from seismic shifts to weather extremes. Although the initial investment in quality concrete may be higher, the potential for long-term savings due to reduced maintenance and repairs often outweighs these upfront costs. For builders and developers, prioritizing quality in concrete is a way to ensure safe, durable structures without frequent intervention for repairs.
How Concrete Quality Affects Durability, Weather Resistance, and Longevity
Concrete is expected to withstand diverse environmental challenges, and New Zealand’s unique climate presents an additional layer of consideration. From coastal salt exposure to regular rainfall and even seismic activity, the materials chosen must be able to resist various weather and geological challenges. High-quality concrete is engineered to be resilient in such varied climates, ensuring the structure’s durability and reducing the risk of premature deterioration.
For instance, concrete quality is a major factor in a building’s resistance to moisture and temperature fluctuations. Low-quality concrete, which may contain impurities or be inadequately mixed, is susceptible to cracking and erosion. In contrast, well-crafted, high-grade concrete resists water intrusion and is more adaptable to temperature changes, crucial for areas experiencing both high humidity and cold snaps. Concrete durability directly correlates with safety and performance; investing in quality ensures buildings can withstand both daily use and severe weather events, maintaining their structural integrity for longer periods.
Long-Term Benefits of Investing in Quality Concrete
While the cost of high-quality concrete may seem like a hefty initial investment, the long-term benefits are undeniable. Structures built with superior-grade concrete require less maintenance, reducing the frequency and cost of repairs over the years. This factor is particularly important in climates like New Zealand, where fluctuating weather and seismic risks can take a toll on building materials. Quality concrete minimizes wear and tear from environmental conditions, meaning fewer repairs and a longer-lasting, more resilient structure.
Not only does quality concrete contribute to lower repair costs, but it also enhances the value of the property itself. Buildings known for structural reliability and low maintenance requirements are more appealing in the real estate market, potentially yielding a higher resale value. For property owners and developers, the initial investment in high-quality concrete can translate into both immediate peace of mind and long-term financial gain.
In conclusion, investing in high-quality concrete isn’t just about ensuring a building’s durability and safety it’s also about making a sound financial choice. The longevity, resistance to weather and environmental stressors, and lower maintenance costs associated with quality concrete make it a wise choice for construction projects in New Zealand and beyond. Prioritizing quality over short-term savings will yield long-term rewards in structural resilience and lower lifetime costs, creating a stable foundation for future generations.
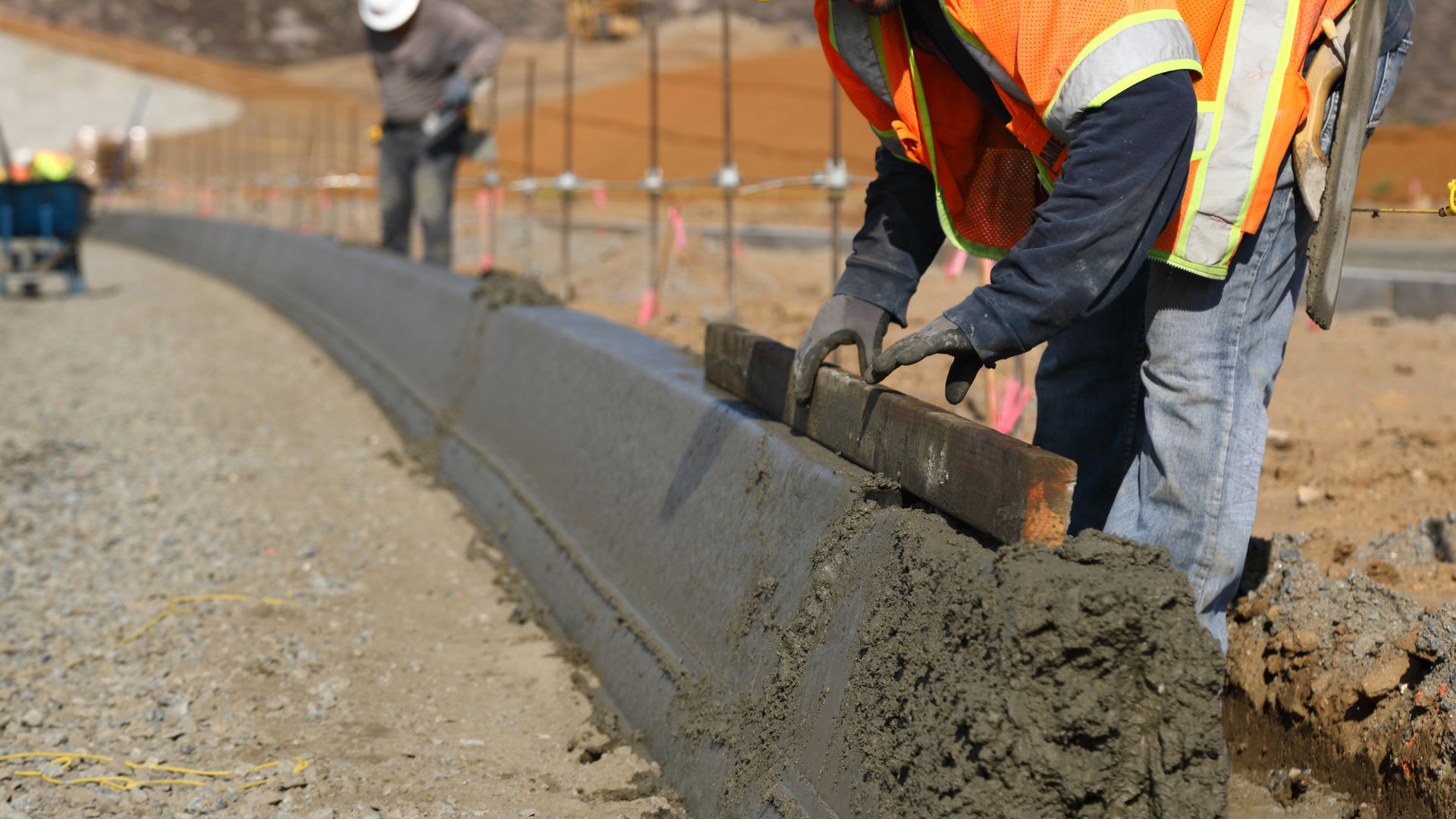
Common Questions About Concrete Pricing In New Zealand
Concrete pricing in New Zealand can be complex, with various factors influencing the final cost. Whether you’re planning a driveway, patio, or foundation, understanding these elements can help you make informed, budget-friendly decisions. Let’s dive into some of the most common questions that homeowners and builders ask about concrete pricing in New Zealand.
Is It Cheaper to Mix My Concrete Than to Order It?
For many, the first question is whether mixing concrete yourself is more cost-effective than ordering ready-mix concrete. Here’s a breakdown of what you need to consider:
- Material Costs: Buying cement, sand, gravel, and water can seem affordable upfront, but prices add up. Small bags of cement, for example, can be significantly pricier per kilogram than bulk purchases included with ready-mix concrete.
- Labor and Time: DIY mixing requires substantial labor, and unless you’re skilled, achieving the right mix consistency and strength can be challenging. Additionally, renting or buying a concrete mixer for large projects can increase costs and complexity.
- Consistency and Quality: Ready-mix concrete, prepared by professionals, ensures consistency, crucial for durability. DIY projects sometimes lack the quality control found in professional mixes, potentially leading to cracks and repairs over time.
In most cases, while DIY may be appealing for small projects, ready-mix concrete is generally a better investment for larger projects or where structural integrity is essential.
How Much Concrete Should I Order for Different Types of Projects?
Estimating the right amount of concrete for your project is essential to avoid waste and keep costs under control. Here are examples of common projects and approximate quantities needed:
- Driveways: Typically, a single-car driveway requires about 1 to 1.5 cubic meters of concrete, depending on the length and width. Double driveways can need around 2.5 to 3 cubic meters.
- Patios: For an average-sized patio (around 10 square meters), plan for about 1 cubic meter of concrete, assuming a standard depth of around 100mm. Larger patios will, of course, need more.
- Foundations: Foundations are critical for structural stability, and depth plays a big role here. A 10-square-meter foundation at a 150mm depth will require approximately 1.5 cubic meters of concrete.
Ordering slightly more than you calculate is often wise, as there can be minor variations in volume, especially for irregularly shaped projects.
Are There Ways to Get Discounts on Concrete?
Concrete is a significant expense, especially for larger projects, so exploring potential discounts can lead to substantial savings. Here are some options to consider:
- Bulk Orders: Many suppliers offer discounts for larger orders, as it reduces delivery trips and improves efficiency on their end. If you’re planning multiple projects, ordering in one go might save you more.
- Regular Customer Discounts: Contractors and builders often receive discounted rates due to their consistent purchasing. If you’re managing a large-scale project, partnering with a contractor may indirectly give you access to these discounts.
- Direct Pick-Up: If feasible, some suppliers offer reduced rates for customers who pick up concrete directly from their facilities. This can be a great option for smaller quantities, though it requires access to appropriate transportation.
In summary, while concrete pricing in New Zealand varies based on project size, complexity, and the type of concrete needed, knowing your options can lead to smarter decisions and potential savings.
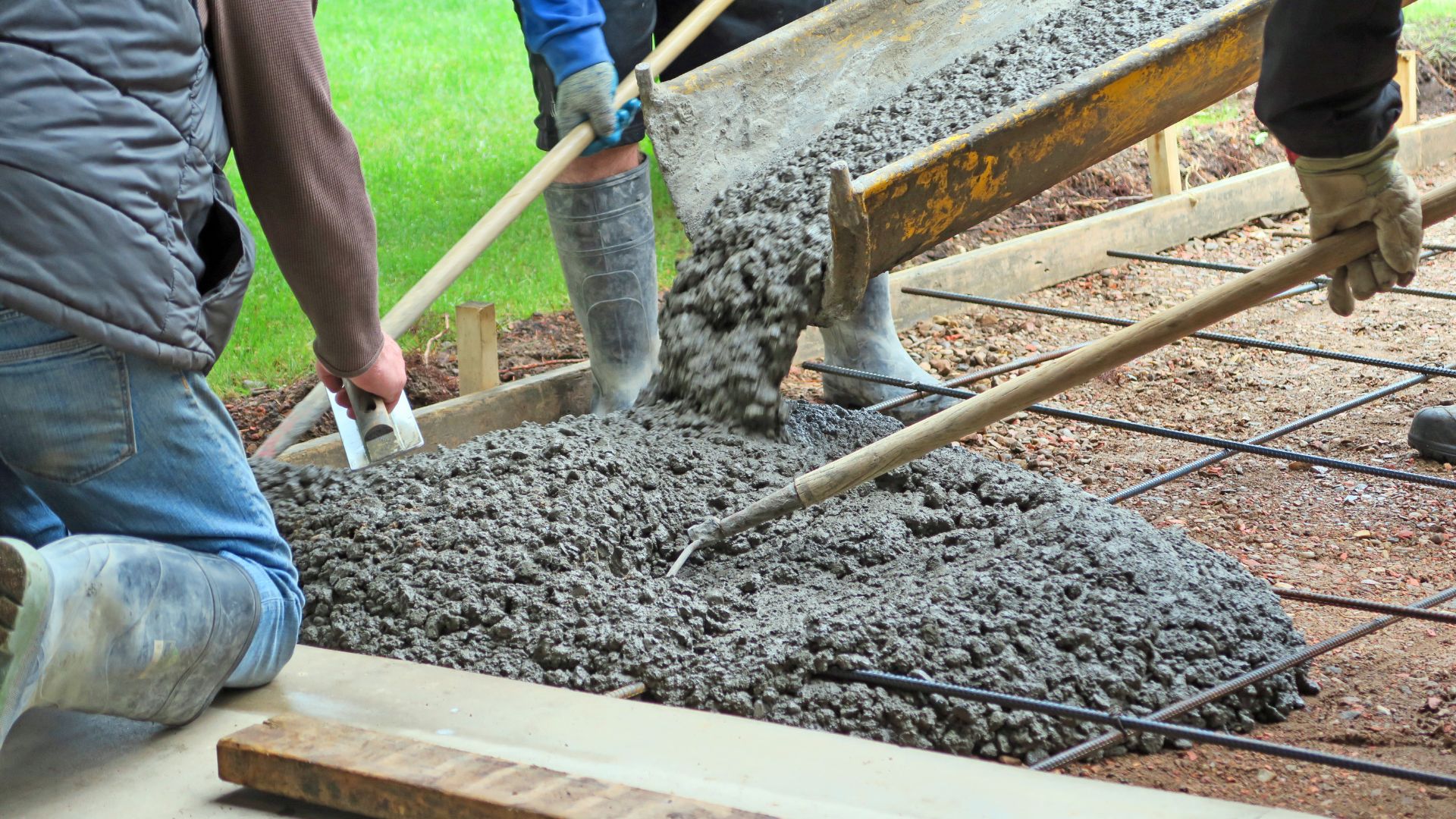
Final Tips For Budgeting And Planning Your Concrete Project
Budgeting for a concrete project is about more than just materials. Every step, from labor to logistics, requires attention to avoid unexpected expenses that can push your project over budget. Here’s how to handle your budget thoughtfully and responsibly, ensuring a smooth process from start to finish.
Calculate All Costs in Advance
When you embark on any concrete project, the initial focus tends to be on the cost of materials alone. However, a successful budget goes beyond just the concrete itself. Here are some areas to consider:
- Concrete Materials: Concrete costs are influenced by mix type, quality, and the amount required. Calculating the total amount of concrete needed will help you gauge initial material costs.
- Delivery Fees: Delivery can be one of the most overlooked costs in concrete projects, particularly if it requires specialized vehicles or additional handling.
- Labor Costs: Labor is a significant part of any concrete project budget. Hourly rates can vary depending on the complexity of the job, regional factors, and the experience level of the crew.
- Extra Costs: Be aware of any unexpected expenses, such as permits, tools, or waste disposal fees. Having a buffer for unforeseen costs keeps you from going over budget.
This comprehensive approach to budgeting prevents surprises and gives you a solid understanding of where your money is going at every stage of the project.
Work with Reputable Suppliers
Concrete projects, whether for residential or commercial purposes, rely on high-quality materials for durability and longevity. Partnering with reputable suppliers offers several benefits:
- Quality Assurance: Established suppliers typically have higher quality standards, ensuring that the concrete mix you receive meets your specifications and durability expectations.
- Reliable Delivery: Reliable suppliers are punctual and have contingency plans for handling delivery delays or weather impacts, saving you time and reducing project disruption.
- Customer Service: Top-rated suppliers are also known for helpful, accessible customer service that makes it easier to troubleshoot, make adjustments to orders, and handle any project-specific requests.
Choosing a supplier known for quality and reliability means fewer delays, lower long-term costs, and peace of mind knowing you have a partner in your project’s success.
Seek Professional Advice if Needed
Not every concrete project requires expert guidance, but if you’re handling a larger or complex job, getting professional input is a wise decision. Consider these aspects where a professional’s expertise can be invaluable:
- Complex Design or Structural Requirements: A larger or intricate project, like a concrete foundation, requires careful engineering to ensure the final structure is safe, sturdy, and aligns with building codes.
- Cost Management: Professionals can offer valuable insight into cost-saving measures, identifying areas where you can reduce expenses without compromising quality.
- Time Efficiency: In larger projects, proper project management is essential. Professional contractors and consultants help ensure that work is completed efficiently, saving you both time and stress.
Investing in expert advice, especially for complex concrete projects, ultimately saves money by helping you avoid costly mistakes and ensuring a high-quality, durable outcome.
By keeping these tips in mind, you’re setting up your concrete project for successful completion within budget, on time, and without compromising on quality. Planning, careful budgeting, reliable partnerships, and professional advice, when needed, are the cornerstones of any well-executed concrete project.
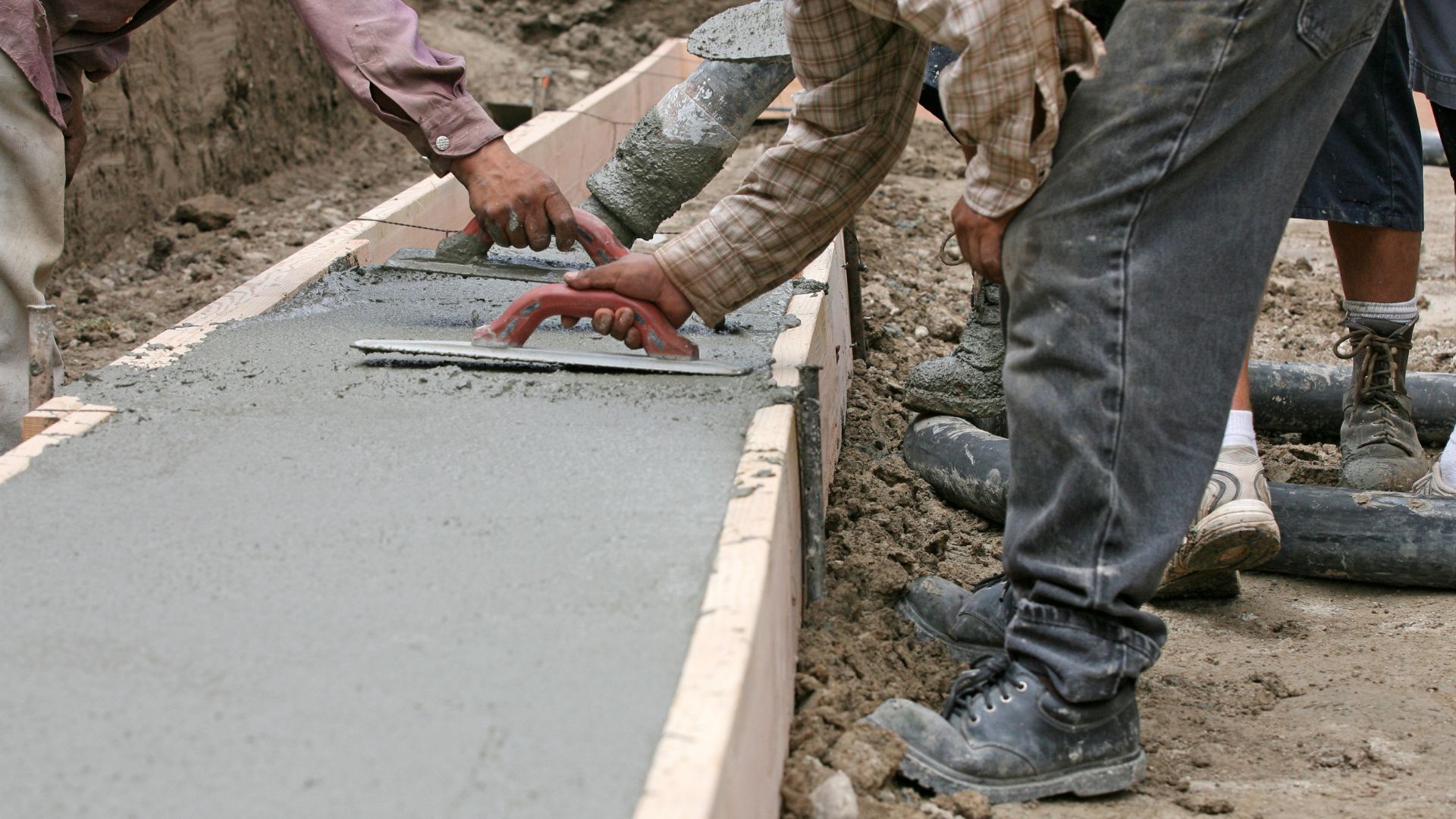
FAQs: About Concrete Price Per M³ NZ
Conclusion
Understanding the pricing of concrete per cubic meter in New Zealand is essential for successful project planning and budgeting. By familiarizing yourself with key factors such as material quality, project scale, and labor costs, you can gain a clear picture of how these elements impact overall expenses. Additionally, considering transportation fees, weather conditions, and timing can help prevent unexpected costs. With a thorough understanding of these factors, you’ll be better equipped to manage expenses effectively and avoid budget overruns. If you’re planning a concrete project, taking the time to get detailed quotes from local suppliers or consulting with industry professionals will ensure a smoother process and higher-quality results. By preparing well and leveraging these insights, you can confidently make informed decisions for your project, ultimately achieving a successful and cost-effective outcome.
About the Author:
Mike Veail is a recognized digital marketing expert with over 6 years of experience in helping tradespeople and small businesses thrive online. A former quantity surveyor, Mike combines deep industry knowledge with hands-on expertise in SEO and Google Ads. His marketing strategies are tailored to the specific needs of the trades sector, helping businesses increase visibility and generate more leads through proven, ethical methods.
Mike has successfully partnered with numerous companies, establishing a track record of delivering measurable results. His work has been featured across various platforms that showcase his expertise in lead generation and online marketing for the trades sector.
Learn more about Mike's experience and services at https://theleadguy.online or follow him on social media: