Welcome to our comprehensive guide on understanding concrete pad costs in New Zealand! Whether you’re planning to build a driveway, patio, or shed base, knowing the costs involved is essential for budgeting and making informed decisions. In this post, we’ll explore the various factors that impact the price of a concrete pad, from the size and type of concrete to labor and site preparation. By the end, you’ll have a clear understanding of what to expect when it comes to the cost of installing a concrete pad in NZ and how to get the best value for your project.
On average, the cost of a concrete pad in New Zealand ranges from $70 to $100 per square meter, depending on factors such as the size, thickness, type of concrete, and site preparation. Additional costs may apply for specialized finishes, reinforcement, and labor, making it essential to get a detailed quote based on your specific project needs.
- What Is A Concrete Pad?
- Factors Affecting Concrete Pad Cost In NZ
- Average Cost Of A Concrete Pad In New Zealand
- DIY Vs. Hiring A Professional For Concrete Pad Installation
- How To Save On Concrete Pad Costs
- Additional Costs To Consider
- Concrete Pad Installation Process: What To Expect
- Common Mistakes To Avoid When Installing A Concrete Pad
- FAQs: About Concrete Pad Cost NZ
- Conclusion
What Is A Concrete Pad?
A concrete pad is a flat, horizontal surface made from poured concrete that serves as a foundation or base for various structures. These pads are commonly used for everything from outdoor patios and garden sheds to larger applications like driveways and garage floors. The concrete is poured into a pre-prepared form, often reinforced with steel or mesh to enhance its strength and durability. Once cured, the result is a stable, durable surface that can handle significant weight and wear, making it an ideal choice for both residential and commercial projects.
Common Applications of Concrete Pads
Concrete pads have a wide range of uses in both residential and commercial settings. In homes, they are commonly installed for outdoor living spaces like patios, where homeowners want a stable, level surface for furniture or barbecues. They’re also frequently used as foundations for smaller structures, such as garden sheds or pergolas. In more heavy-duty applications, concrete pads are popular for driveways, offering a strong and long-lasting solution to withstand the weight of vehicles. Commercially, concrete pads are often utilized in parking lots, industrial storage areas, and even as a base for large machinery.
Difference Between a Concrete Pad and Other Foundations
It’s important to distinguish a concrete pad from other types of foundations, such as concrete slabs. While both are made from poured concrete, they differ primarily in terms of depth and purpose. A concrete slab is generally much thicker and is used to support entire buildings, often acting as a structural foundation. Slabs typically include footings—reinforced edges designed to bear the weight of the walls and roof. A concrete pad, on the other hand, is usually thinner and is not always intended to bear the load of a full structure. Pads are more often used for surface-level projects like walkways, patios, or smaller storage sheds, where the weight is more distributed.
Benefits of Choosing a Concrete Pad
Concrete pads offer a variety of benefits that make them an excellent choice for both residential and commercial applications. One of the primary advantages is durability—concrete pads can last for decades with minimal maintenance, providing a solid foundation for any structure placed on top. They are also highly versatile, capable of being customized with different finishes, such as stamped or exposed aggregate, to match the aesthetic of a home or business. Additionally, concrete pads offer superior resistance to weather, making them particularly suitable for New Zealand’s climate. Unlike wooden foundations, concrete doesn’t rot, warp, or deteriorate over time. Lastly, they offer excellent cost-efficiency. A concrete pad is relatively quick to install, especially for small-scale projects, and the upfront costs are often lower compared to other foundation types like slabs or footings, making them a practical and economical choice.
By understanding what a concrete pad is, its differences from other foundation types, and the benefits it provides, you can make an informed decision about whether it’s the right option for your next project. Whether you’re looking to build a new driveway, install a patio, or create a foundation for a garden shed, a concrete pad offers a sturdy, long-lasting solution that suits a variety of needs.
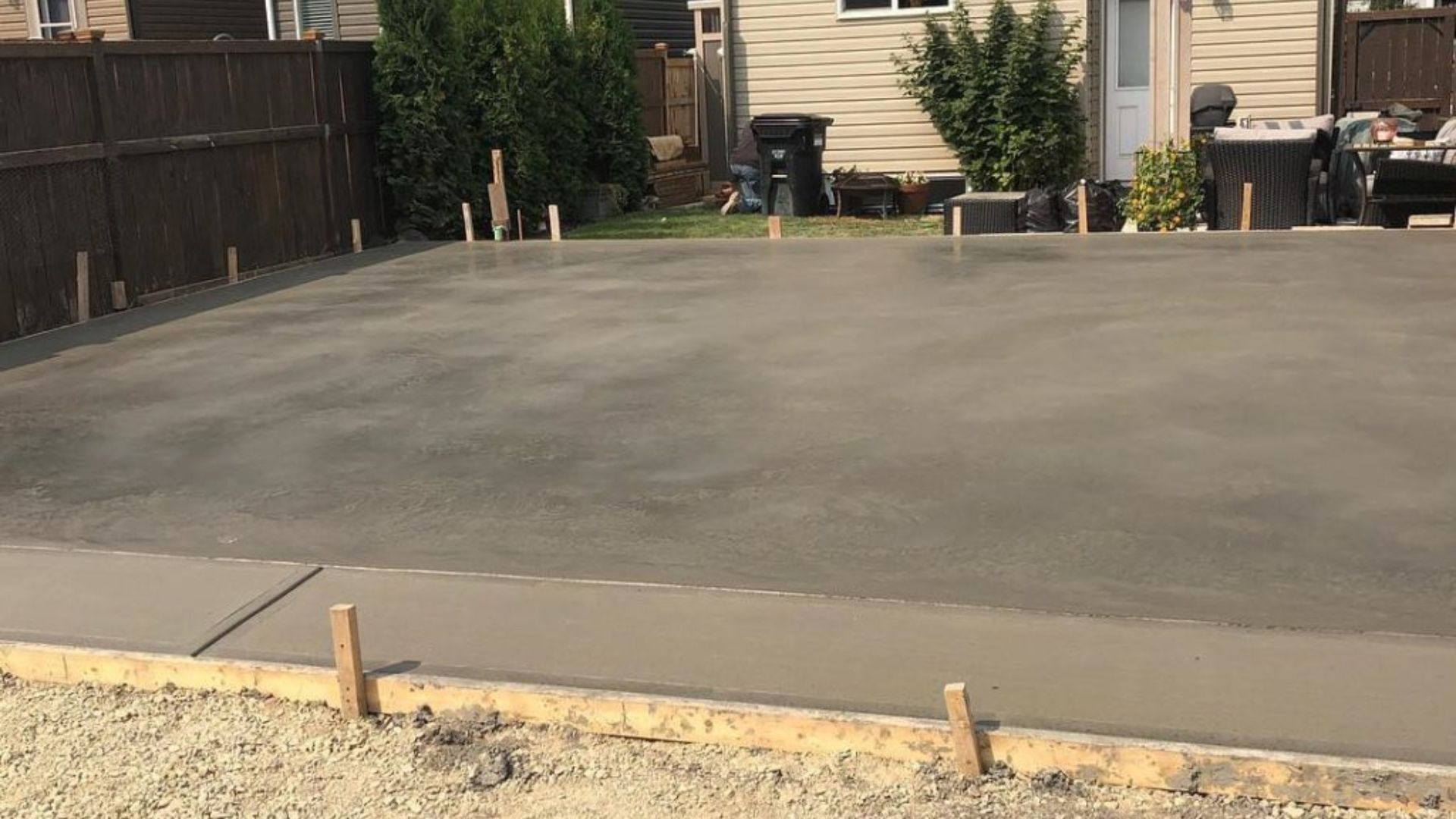
Factors Affecting Concrete Pad Cost In NZ
When planning for a concrete pad project in New Zealand, several critical factors impact the overall cost. Understanding these variables can help you budget more effectively and avoid surprises down the line. Here’s a detailed look at each factor that influences concrete pad costs.
Size of the Pad
The size of the concrete pad is one of the most significant cost determinants. Larger pads naturally require more materials and additional labor, which increases the total expense. For example, a small concrete pad for a garden shed will be far less expensive than a large one for a driveway or a garage base. The cost per square meter often decreases with larger pads due to economies of scale, but the overall cost will still be higher. Typical concrete pad sizes can range from a small 3×3 meter pad for minor projects, costing around $600–$900, to much larger pads for driveways, which can cost thousands depending on the total area.
Thickness and Reinforcement
The thickness of the concrete pad is another essential factor. Thicker pads require more concrete, raising material costs. For standard use, such as a backyard patio or walkway, a thickness of around 75mm is common, but for heavier loads—like a garage floor or a driveway that will support vehicles—you may need a thicker pad, often around 100mm or more. Additionally, reinforced concrete, which includes steel mesh or rebar, adds to both the strength and the cost. Reinforcement is crucial for pads that will bear significant weight, such as those under garages or heavy machinery, as it prevents cracking and ensures long-term durability. While this will increase the cost upfront, it’s a necessary investment for structural integrity in many cases.
Type of Concrete
The type of concrete you choose also plays a significant role in the final cost. Standard concrete is generally the most affordable option, but there are more decorative finishes available, which can drive up the price. For example, exposed aggregate or stamped concrete provides a more aesthetically pleasing surface, but these finishes come at a premium. Decorative concrete is popular for patios, driveways, and outdoor spaces where appearance is just as important as function. In contrast, for utilitarian purposes like a shed base or a foundation for a structure that won’t be seen, opting for standard concrete can save you money. The mix of concrete can also influence cost; higher-grade mixes designed for heavy-duty applications will naturally be more expensive than basic mixes.
Site Preparation
Before any concrete can be poured, proper site preparation is essential, and this can add to the overall cost of the project. Site preparation involves clearing the area of any vegetation, debris, or existing structures, leveling the ground, and sometimes even adding a gravel base for better drainage. If your site has sloping terrain or other challenges, the cost of preparing the site will increase. For example, a flat, easily accessible area will be much cheaper to prepare than a sloped or hard-to-reach location. Additionally, if excavation is required, this will add to both labor and equipment costs. Site preparation is crucial for ensuring that the concrete pad is laid on a solid, even foundation, which prevents future issues like cracking or sinking.
Location
Where you’re located in New Zealand can significantly affect both material and labor costs. Urban areas like Auckland, Wellington, and Christchurch often have higher labor costs due to increased demand and living expenses, while rural areas might see lower rates but could incur additional transportation costs. If your site is far from suppliers or contractors, you may need to account for extra delivery fees for materials, such as concrete and reinforcement materials. Additionally, labor costs can be higher in remote areas if it requires contractors to travel long distances or stay on-site for extended periods. It’s important to factor in location-based price differences when budgeting for your concrete pad project.
Labor Costs
Labor is a substantial part of the overall cost of installing a concrete pad. The rates for professional concrete layers in New Zealand vary, but you can expect to pay anywhere from $50 to $100 per hour, depending on the complexity of the job and location. Larger projects may involve a team of workers, which can increase the hourly labor costs but reduce the overall project timeline. Labor costs also include the time taken for tasks such as site preparation, pouring the concrete, finishing the surface, and ensuring the concrete cures correctly. Hiring a professional ensures the job is done right the first time, reducing the risk of future costly repairs.
Permits and Regulations
In some cases, obtaining a building permit is required before you can install a concrete pad, especially for larger or more complex projects. Permit costs vary depending on your local council’s regulations, but they typically range from $100 to $500, depending on the scope of the project. It’s essential to check with your local council to see if your project requires a permit, as failing to comply with building regulations can result in fines or the need to remove and rebuild the pad. Compliance with New Zealand building standards is crucial, particularly if your concrete pad is part of a larger construction project like a new home or a commercial structure. Additionally, for certain projects like driveways that connect to public roads, additional approvals or requirements may be necessary, which could also influence the overall cost.
By understanding the key factors that affect the cost of a concrete pad in New Zealand, you can better plan and budget for your project. Whether you’re installing a simple garden shed base or a large, reinforced driveway, taking these variables into account will help ensure that your concrete pad is both cost-effective and built to last.
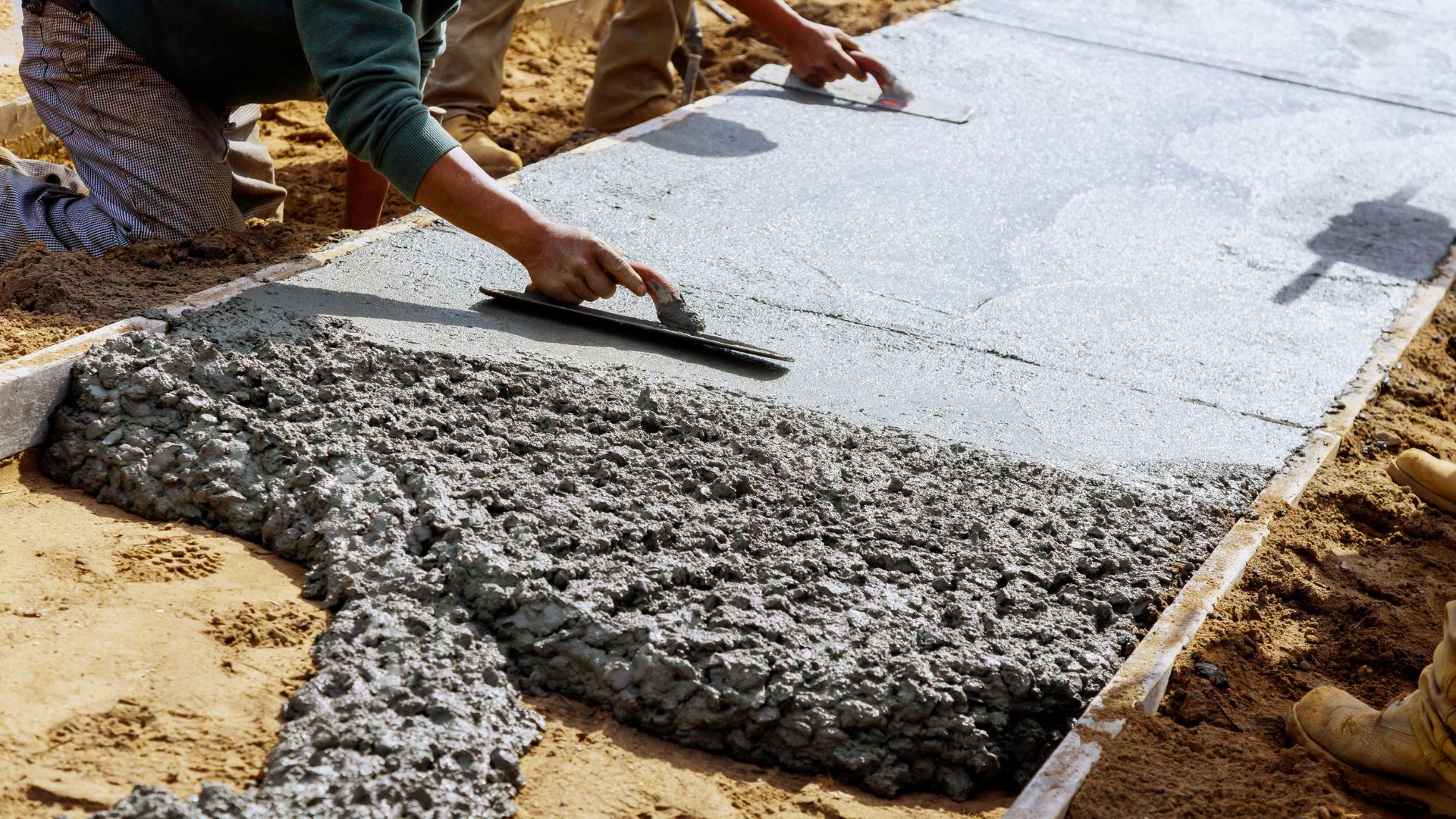
Average Cost Of A Concrete Pad In New Zealand
When planning to install a concrete pad, understanding the average cost is crucial for budgeting and ensuring you get the best value for your money. In New Zealand, the cost of a concrete pad can vary based on several factors, including the size of the pad, the thickness of the concrete, the type of finish you choose, and even your location. Below is a detailed breakdown of the typical costs you can expect for different types of concrete pad projects.
Cost per Square Meter
On average, the cost of a concrete pad in New Zealand ranges between $70 to $100 per square meter. However, this price is not set in stone and can fluctuate depending on a few key factors:
- Thickness: A standard concrete pad with a thickness of 75mm (suitable for lighter loads like patios or walkways) will generally be on the lower end of the cost spectrum. However, for driveways or areas that will bear heavier loads, a thickness of 100mm or more may be necessary, which can increase the price.
- Finishes: The finish you choose for your concrete pad also plays a significant role in determining the cost. A basic, smooth finish is usually the most affordable option, but if you’re looking for something more decorative like exposed aggregate or a stamped design, expect to pay more. Decorative finishes not only enhance the aesthetic appeal of your pad but also increase the price per square meter due to the additional materials and labor involved.
- Location: The cost of a concrete pad can also vary depending on where you live in New Zealand. Urban areas, where contractors and materials are more readily available, may offer more competitive pricing compared to rural regions where transportation costs for materials and labor may drive the price up.
Typical Price for Common Projects
The type of project you’re undertaking also influences the overall cost of a concrete pad. Here’s a breakdown of typical costs for common projects:
Concrete Pad for a Driveway
A concrete driveway is one of the most popular applications for concrete pads. For a standard driveway, you can expect the cost to range from $100 to $130 per square meter. Driveways usually require thicker concrete (100mm or more) to support the weight of vehicles, which increases the material and labor costs. Additionally, many homeowners opt for reinforced concrete for extra durability, which further adds to the price.
Concrete Pad for a Shed
If you’re laying a concrete pad for a shed, the costs are typically lower compared to a driveway. A shed pad doesn’t need to bear as much weight, so a 75mm to 100mm thick pad is usually sufficient. The cost for a shed pad generally ranges between $80 and $110 per square meter. Depending on the size of the shed and whether the site requires any extra leveling or preparation, this price could vary.
Concrete Pad for Patios and Outdoor Areas
Patios and outdoor living spaces are another common use for concrete pads. These spaces generally don’t require as much thickness as driveways, so the cost is often on the lower end of the spectrum. You can expect to pay around $70 to $100 per square meter for a basic patio pad. If you choose to go for decorative finishes, like exposed aggregate or colored concrete, this could push the price up towards the higher end or beyond.
The cost of a concrete pad in New Zealand can vary significantly depending on the size, thickness, finish, and location of your project. Whether you’re laying a pad for a driveway, shed, or patio, it’s important to plan your budget accordingly. Always get multiple quotes from contractors, and be sure to consider the long-term durability and aesthetic value of investing in higher-quality finishes and materials.
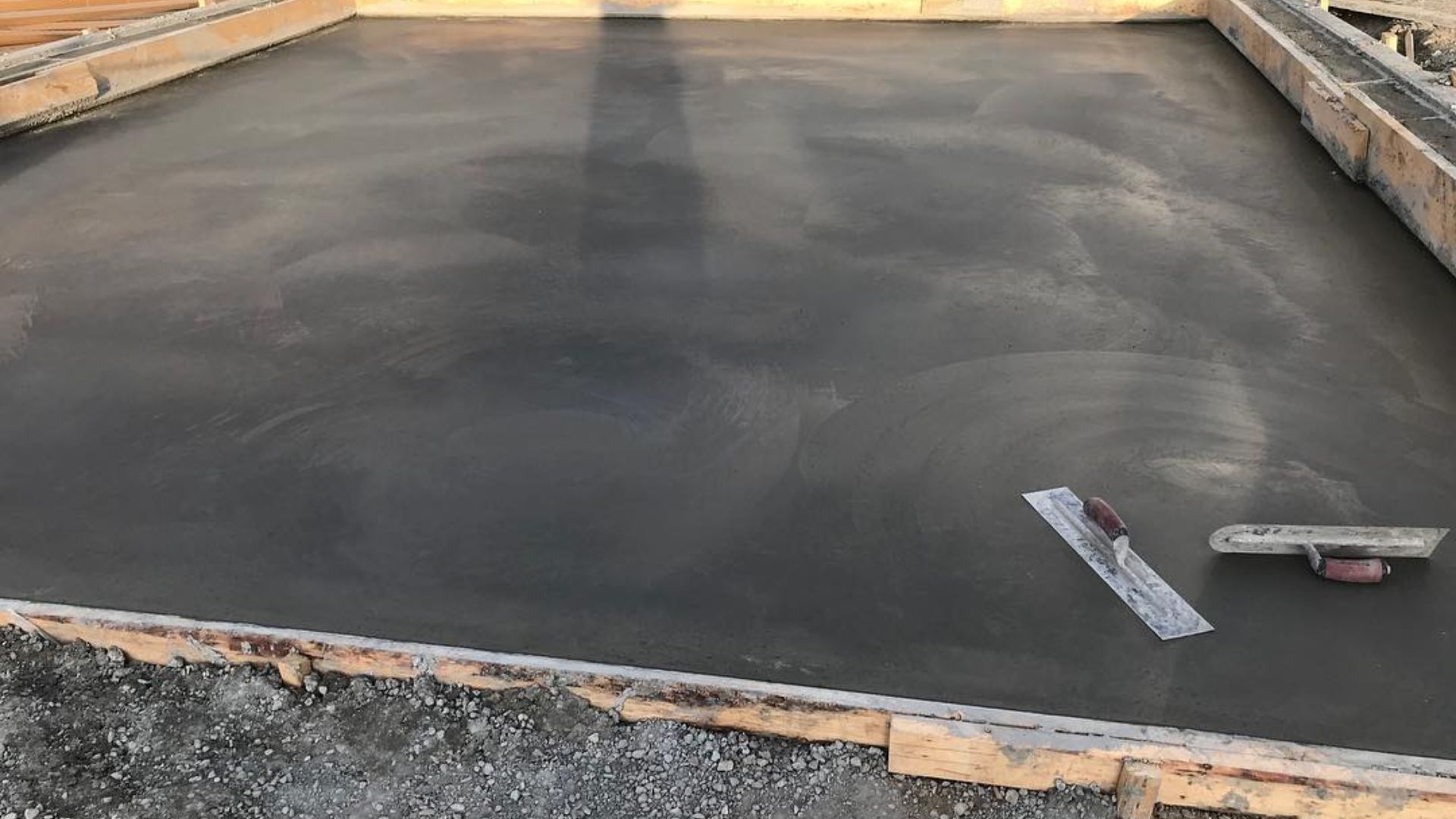
DIY Vs. Hiring A Professional For Concrete Pad Installation
When it comes to installing a concrete pad, one of the most important decisions you’ll need to make is whether to tackle the project yourself or hire a professional. Both options have their advantages and drawbacks, so it’s crucial to weigh the cost, effort, and risks involved before making your choice.
DIY Concrete Pad: Is It Worth Doing It Yourself?
Taking the DIY route for installing a concrete pad can seem appealing, especially when considering potential cost savings. By eliminating labor costs, which can account for a significant portion of your overall budget, you might be able to save a substantial amount of money upfront. For a small concrete pad, such as a patio or shed base, DIY could be a viable option, particularly if you have some experience in construction or are comfortable with hands-on projects.
However, while cost savings are enticing, DIY concrete work requires careful consideration of the tools, materials, and skills needed to execute the job properly. Here’s what you should know.
- Tools and Materials Required: To successfully lay a concrete pad yourself, you’ll need specific tools such as a concrete mixer, trowels, shovels, leveling tools, and form boards. Additionally, purchasing concrete mix, gravel, rebar (if reinforcement is needed), and sealants are essential materials for the project. These tools and materials can add up in cost if you don’t already have them on hand.
- Potential Challenges: Even with the right tools, installing a concrete pad is a physically demanding and technical task. One of the biggest challenges for DIYers is ensuring that the pad is properly leveled and adequately prepared before pouring the concrete. Without experience, it’s easy to overlook critical factors like ground preparation, drainage, and proper curing, which could lead to long-term problems like cracks or uneven surfaces.
- Risks Involved: DIY concrete work comes with several risks. Improper leveling, for example, can cause water drainage issues or an unstable foundation. Cracking can occur if the concrete isn’t mixed properly or if it’s not allowed to cure correctly. Curing, the process by which concrete hardens, takes time and requires specific conditions (such as consistent moisture levels) to ensure a durable result. If these factors aren’t managed properly, you might face costly repairs down the road, negating any initial savings.
Hiring a Professional: Why It Might Be Worth the Investment
While DIY can save on labor costs, hiring a professional contractor for your concrete pad installation offers several significant advantages, especially for larger or more complex projects like driveways or garage foundations. Here’s why.
- Quality and Durability: Professional concrete contractors have the experience, knowledge, and equipment to ensure the job is done right the first time. From properly leveling and preparing the site to ensuring the concrete is mixed and poured correctly, a professional will ensure that your concrete pad is strong, durable, and built to last. This reduces the risk of costly repairs or replacements later on.
- Compliance with Regulations: Depending on your location in New Zealand, there may be specific building codes or regulations that must be followed when installing a concrete pad. A licensed contractor will be familiar with local rules and ensure your project meets all compliance standards, which is especially important for pads supporting structures like garages or sheds.
- Choosing a Reliable Contractor: Finding the right contractor is key to getting high-quality results. When selecting a contractor, check their qualifications, including licensing, insurance, and experience with similar projects. Request references or look for reviews from previous clients to gauge their reliability. It’s also a good idea to get multiple quotes to ensure you’re getting a fair price and an accurate estimate for your project.
- What to Expect During the Process: Once you’ve hired a professional, the installation process typically begins with a site inspection. The contractor will assess the area where the pad will be installed, check for any issues that need to be addressed (such as grading or drainage), and discuss the project timeline. After agreeing on the scope of work, the contractor will provide a quote, which should include labor, materials, and any additional costs such as permits or reinforcement.
The timeline for professional concrete pad installation depends on the size of the project but generally includes site preparation, pouring the concrete, and allowing the pad to cure. Professionals understand how to manage the curing process to ensure long-lasting strength, and they can also offer advice on ongoing maintenance to maximize the lifespan of your concrete pad.
Final Considerations: DIY vs. Hiring a Professional
Ultimately, deciding between DIY and hiring a professional comes down to the size and complexity of your project, your budget, and your confidence in handling the task. For smaller projects, DIY may provide reasonable savings, but it’s essential to be aware of the risks and potential complications. On the other hand, hiring a professional is generally the best option for larger pads or when you want to ensure high-quality, compliant work that will stand the test of time.
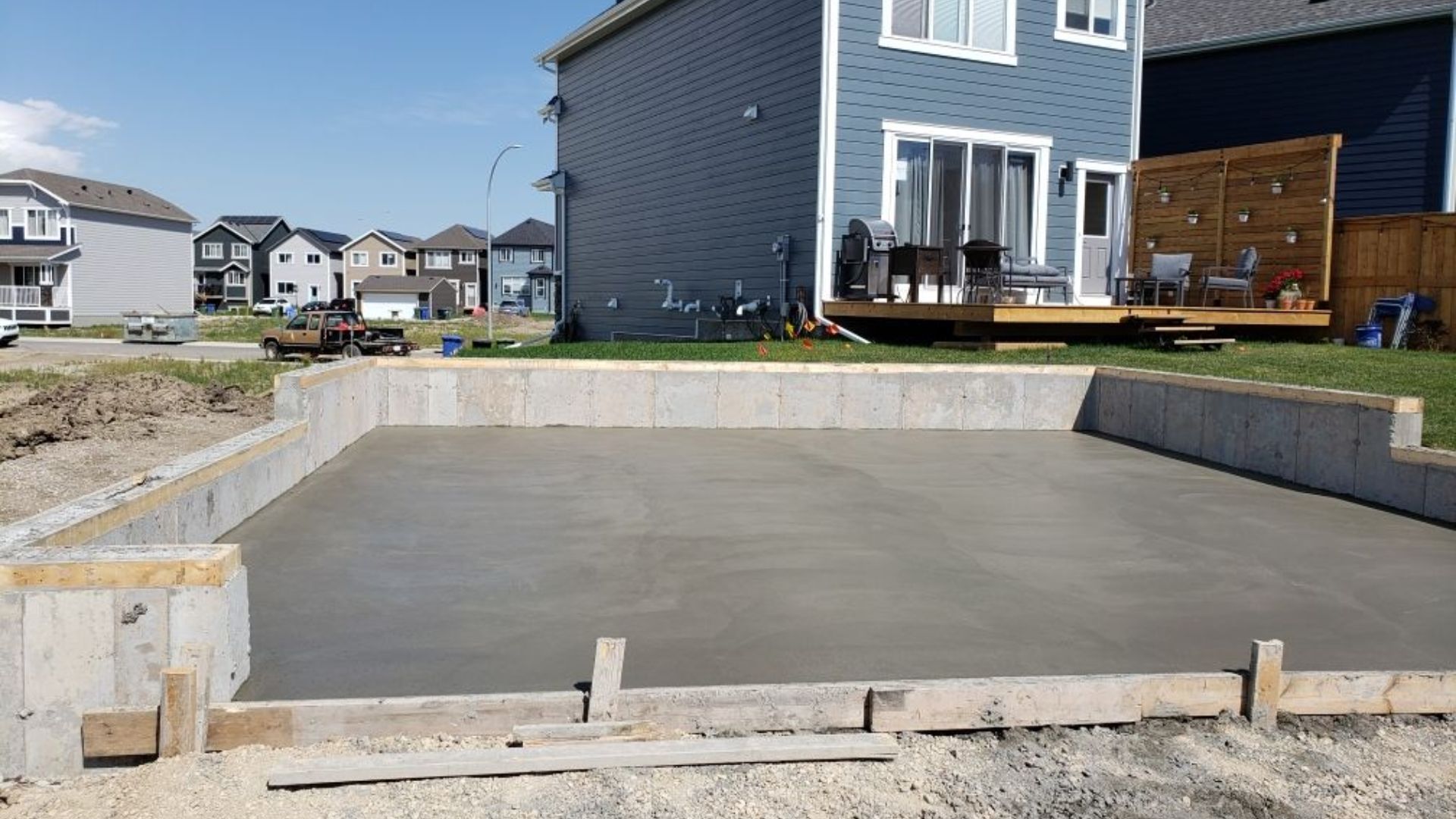
How To Save On Concrete Pad Costs
When planning to install a concrete pad in New Zealand, costs can add up quickly, but there are several ways to save without compromising on quality. From careful planning to smart choices on materials and timing, you can significantly reduce expenses. Below, we’ll discuss some practical strategies to help you keep your concrete pad project within budget.
Plan Ahead
Proper planning is the cornerstone of saving money on any construction project, and concrete pads are no exception. By thoroughly planning every aspect of your project, you can avoid costly surprises and ensure you stay within budget. Start by determining the size and scope of the concrete pad you need. Whether it’s for a driveway, patio, or shed foundation, having clear specifications upfront allows contractors to give you accurate quotes.
One of the key steps in planning ahead is getting multiple quotes from reputable contractors. Don’t settle for the first quote you receive; instead, take the time to compare services, materials, and prices. Different contractors may offer various solutions, and by comparing options, you can identify where you can save without compromising on quality. Ask for itemized quotes so you can clearly see what you’re paying for labor, materials, and any extras.
Additionally, discuss with your contractor any potential challenges at the site that could drive up costs, such as difficult access, drainage issues, or soil that requires extra preparation. By addressing these issues during the planning stage, you avoid unexpected expenses that could blow your budget.
Choose the Right Time
The timing of your project can also play a significant role in how much you end up spending on your concrete pad. In New Zealand, the demand for contractors typically rises during the warmer months when outdoor projects are more common. As a result, rates for labor and materials can be higher during these peak periods.
To save money, consider scheduling your project during the off-peak season. Contractors may be more willing to offer discounts when business is slower, and material suppliers may also have lower prices outside the high-demand months. However, it’s essential to balance cost savings with practical considerations like weather conditions, as pouring concrete in extremely wet or cold conditions could affect the quality and durability of your pad.
Optimize Materials and Design
Another way to control costs is by carefully choosing your materials and design. Concrete comes in various types and finishes, and while high-end finishes like exposed aggregate or stamped concrete can look stunning, they come at a premium. If aesthetics aren’t your primary concern, opting for a standard finish can help you stay within your budget.
When discussing material options with your contractor, ask about alternative concrete mixes that offer durability without inflating the cost. For instance, some contractors may suggest adding reinforcement only where necessary, rather than throughout the entire pad, which can lower material expenses without sacrificing structural integrity.
Similarly, the design of your concrete pad can have a significant impact on the total cost. A more complex design with curves, edges, or unique shapes can require more labor and materials, which will drive up the price. Simplifying the design—such as opting for a basic rectangular pad—can result in significant savings. Always balance your functional needs with cost considerations to avoid overspending on unnecessary design elements.
Combine Projects
If you have multiple concrete projects on your property, bundling them together can be a cost-effective strategy. For example, if you’re planning to pour a concrete pad for a driveway and a patio, having the contractor complete both projects at the same time can save on labor costs, as the contractor won’t need to bring equipment and crew back on different occasions.
Bulk ordering materials like concrete also becomes more economical when completing several projects at once. Contractors are more likely to offer discounts when they can work on larger projects, reducing overhead and transportation costs. Even if you’re only considering one project at the moment, it’s worth thinking ahead—if you plan to add more concrete structures in the near future, bundling them could save you money in the long run.
Saving on concrete pad costs in New Zealand doesn’t have to mean cutting corners. By planning ahead, selecting the right timing, optimizing materials and design, and combining projects, you can keep your costs down while ensuring a high-quality result. Taking a strategic approach not only helps you stay within budget but also ensures the durability and longevity of your concrete pad, making it a sound investment for your property.
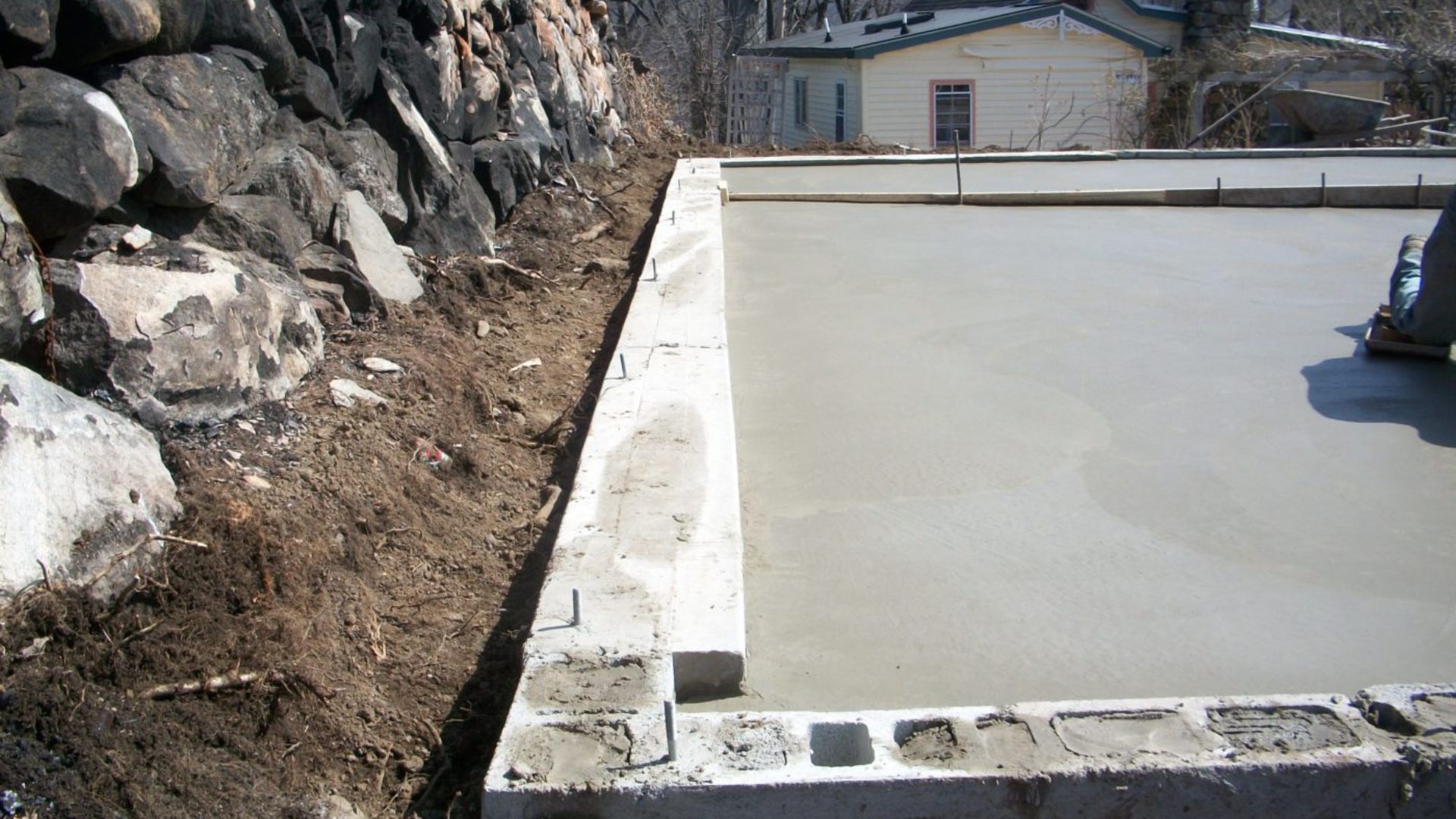
Additional Costs To Consider
When planning for a concrete pad, it’s easy to focus solely on the upfront expenses like materials, labor, and installation. However, several additional costs often arise that you’ll need to factor into your budget. These costs can ensure the longevity and functionality of your concrete pad, protecting your investment in the long run.
Drainage Solutions
One critical yet sometimes overlooked factor is proper drainage. Without an efficient drainage system, water can accumulate around or under the concrete pad, leading to erosion, cracks, and long-term damage. Water buildup weakens the structural integrity of the concrete, causing it to degrade faster than it should. This is particularly important for areas prone to heavy rainfall, as water that cannot drain properly will sit, increasing the likelihood of damage.
Installing drainage solutions, such as drainage channels or gravel layers beneath the pad, can prevent these issues, but they do come at an additional cost. Depending on the complexity of the drainage system needed, this could add anywhere from a few hundred dollars to several thousand to the overall project budget. The cost will vary based on your site’s natural drainage capacity, soil type, and the size of the concrete pad. Investing in proper drainage upfront can save you from expensive repairs or replacements down the road, making it a wise addition to your budget.
Sealing and Maintenance
Another vital cost to consider is sealing the concrete pad. Sealing acts as a protective layer that shields the concrete from harsh weather conditions, moisture, and stains. In New Zealand’s variable climate, where you might face everything from heavy rains to strong UV exposure, a good sealant is essential. Over time, unsealed concrete can absorb water, which expands during freezing conditions, leading to cracks or surface degradation. Additionally, oils, chemicals, and other materials can easily stain unsealed concrete, diminishing its appearance and potentially reducing its lifespan.
The cost of sealing a concrete pad typically depends on the size of the area and the type of sealant used. Generally, sealing a concrete pad costs between $10 and $20 per square meter. Though this is an extra expense, it significantly extends the lifespan of your concrete pad, reducing the need for costly repairs. Sealing is not a one-time expense; you’ll need to reseal the pad every few years to maintain its protection. Routine cleaning is also necessary to prevent dirt and debris from accumulating, which can lead to surface damage. Budgeting for occasional professional resealing, along with regular cleanings, is a smart way to keep your concrete pad in top condition.
Potential Repairs or Expansion in the Future
As with any structure, even a well-installed and maintained concrete pad may require repairs or expansion in the future. Over time, cracks or small surface imperfections may appear due to weather conditions, ground movement, or heavy usage. While minor cracks can often be repaired relatively easily, major damage could require more extensive repairs, including resurfacing or partial replacement, which can be more costly.
If you’re considering expanding the pad in the future—perhaps to accommodate more vehicles or extend your outdoor area—this will involve additional costs. Expansion may require the same groundwork as the initial installation, including excavation, new materials, and labor. Depending on how large the expansion is, it could cost nearly as much as the original pad, especially if there are complications like uneven terrain or difficulty matching the existing concrete.
While the initial installation of a concrete pad is a significant investment, accounting for additional costs like drainage, sealing, maintenance, and potential future repairs or expansions is essential for budgeting properly. These expenses ensure that your concrete pad remains durable, functional, and attractive for years to come.
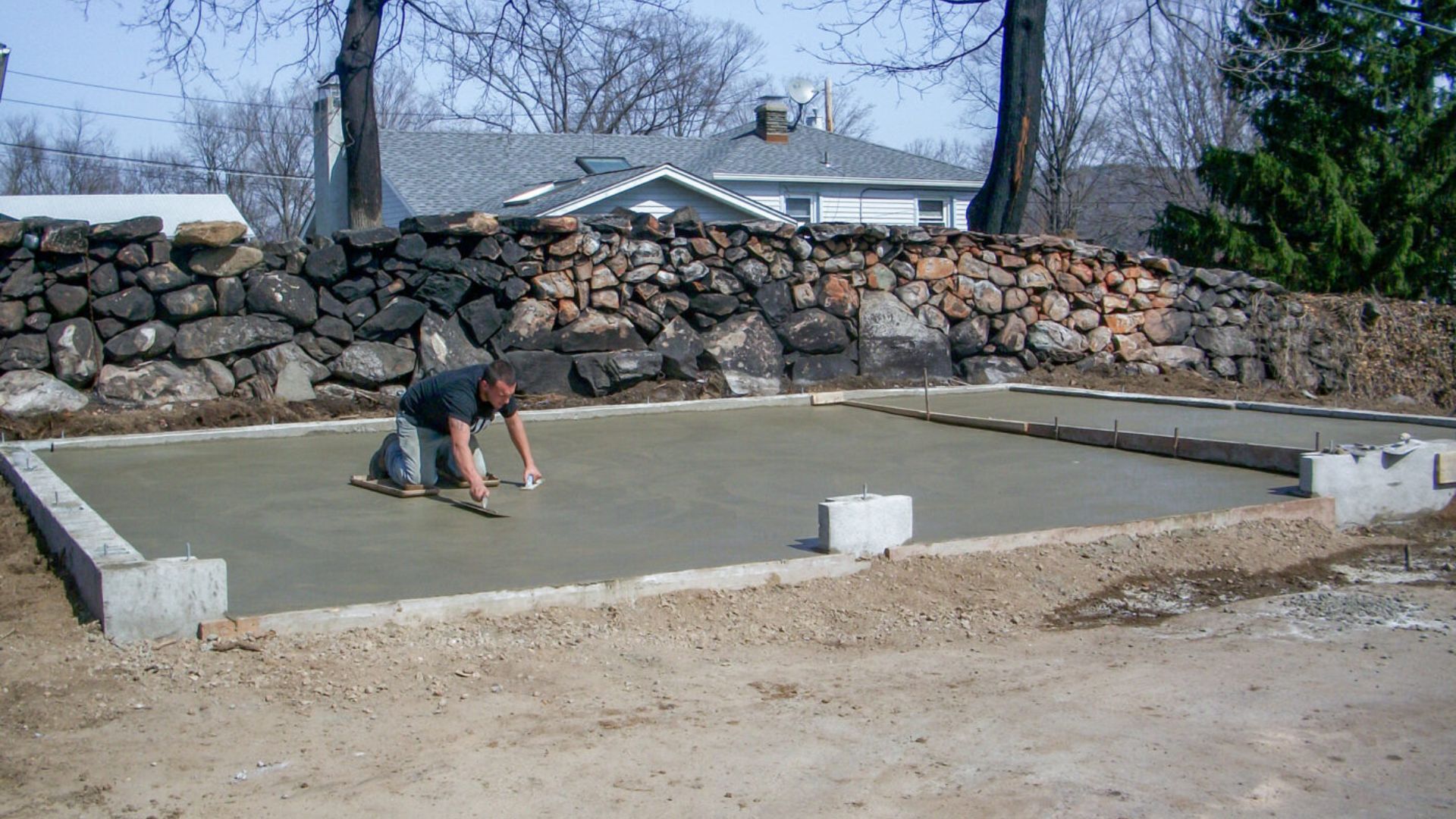
Concrete Pad Installation Process: What To Expect
When planning to install a concrete pad, understanding the entire process can help you prepare and ensure a smooth, successful project. The installation typically involves three key stages: initial site preparation, laying the concrete, and post-installation care. Each step is crucial to ensuring the durability and longevity of your concrete pad. Here’s a detailed breakdown of what you can expect during the installation process:
Initial Site Preparation
Before any concrete is poured, the site needs to be thoroughly prepared. Proper site preparation is essential because it lays the foundation for a level, stable, and long-lasting concrete pad. Here’s how it works.
1. Clearing the Site
The first step is clearing the area where the concrete pad will be installed. This includes removing any vegetation, rocks, debris, or old structures that may be in the way. If there are trees or shrubs in the area, their roots might need to be removed to prevent future damage to the concrete.
2. Leveling the Ground
Once the site is cleared, the ground must be leveled. This is a critical step because an uneven surface can lead to cracking or water pooling on the concrete pad over time. Professional contractors will often use tools such as laser levels or grading equipment to ensure the surface is perfectly flat and slopes slightly away from structures to aid in water drainage.
3. Adding a Sub-Base
In many cases, a sub-base layer (such as gravel or crushed stone) will be added to provide extra stability. This sub-base helps with drainage and prevents soil shifting underneath the pad. The layer is usually compacted using heavy machinery to create a solid foundation for the concrete.
Laying the Concrete
With the site prepared, the actual concrete pouring process begins. This is where precision and timing come into play to ensure the concrete pad cures correctly and without issues.
1. Formwork Setup
Before pouring the concrete, formwork is installed. These are temporary frames, typically made of wood or metal, that hold the concrete in place while it cures. The formwork defines the shape and edges of the concrete pad and ensures that the poured concrete stays within the desired dimensions.
2. Mixing and Pouring the Concrete
Once the formwork is set, the concrete mix is prepared. For larger jobs, contractors usually have ready-mix concrete delivered in trucks, but for smaller projects, concrete can be mixed on-site. The concrete is then poured into the formwork, starting from one end and working systematically to ensure even distribution.
3. Leveling and Smoothing the Surface
After the concrete is poured, it needs to be leveled and smoothed using tools like a screed or trowel. This ensures the surface is even and free from air pockets that could weaken the pad. In some cases, contractors might also apply a float finish or broom finish for additional texture, which can improve traction for outdoor surfaces like driveways.
4. Reinforcement and Finishing
If the concrete pad is meant to bear heavy loads, such as for a garage or driveway, reinforcement like steel rebar or wire mesh might be added to improve its strength. Finally, any decorative finishes, such as stamping or exposed aggregate, will be applied if requested by the homeowner.
Post-Installation
Once the concrete is poured and finished, the work doesn’t stop there. The post-installation phase is crucial for ensuring the pad’s durability and proper curing.
1. Curing Time
Curing is the process through which concrete gradually hardens and gains strength. Typically, concrete requires around 24 to 48 hours to set enough that it can support light foot traffic. However, it takes about 28 days to fully cure. During this time, it’s important to keep the surface moist, especially during the first week, as this helps the concrete cure evenly and prevents cracking. A common method is covering the pad with damp burlap or applying a curing compound.
2. When Can Concrete Be Used
Light foot traffic is usually possible after 48 hours, but for heavier loads like vehicles, you’ll need to wait at least a week or longer, depending on the weather and curing conditions. For driveways, garages, or pads supporting heavy structures, it’s typically recommended to wait 7 to 10 days before use. Full strength will be achieved by the end of the 28-day curing period, after which the concrete pad can be fully utilized.
3. Post-Curing Maintenance
After the curing process, homeowners should consider sealing the concrete to protect it from the elements, especially if it’s an outdoor pad exposed to weather. Sealers can prevent moisture infiltration, minimize cracking, and protect the surface from stains or damage caused by freeze-thaw cycles. Regular maintenance, like cleaning and resealing every few years, can extend the life of the pad significantly.
Installing a concrete pad is a detailed process that requires careful planning and execution. From preparing the site and pouring the concrete to allowing it to cure properly, each step plays a vital role in ensuring the final product is strong and durable. Homeowners should work closely with their contractors to understand the timeline and post-installation care needed to keep the concrete in top shape for years to come. By following these steps, you can ensure that your concrete pad will be a solid, long-lasting addition to your property.
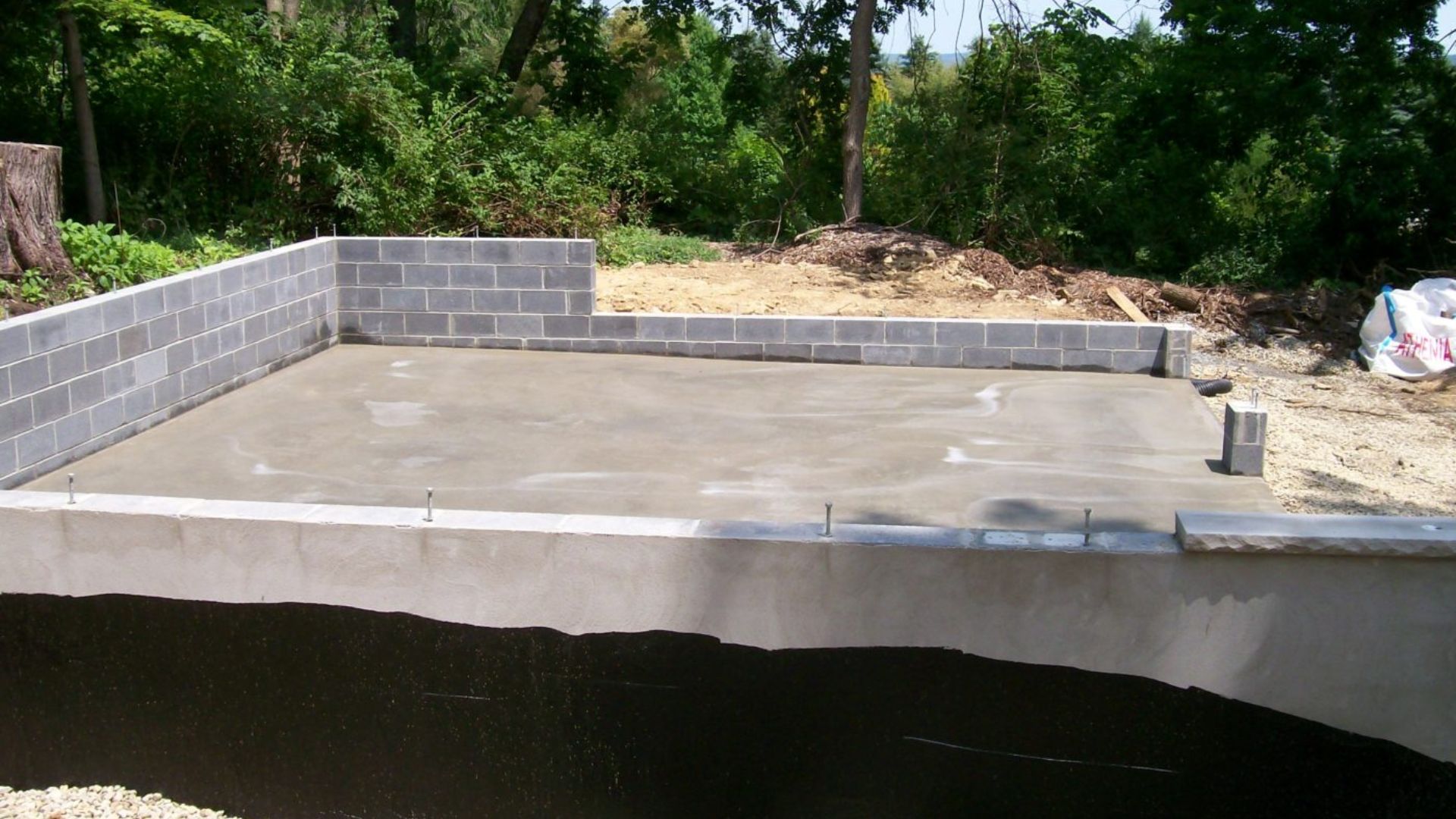
Common Mistakes To Avoid When Installing A Concrete Pad
When installing a concrete pad, avoiding certain common mistakes can make the difference between a durable, long-lasting structure and one that requires frequent repairs or fails prematurely. These errors not only affect the integrity of the concrete pad but also increase long-term costs and reduce overall satisfaction with the project. Below are the key mistakes to watch out for and how to avoid them.
Skimping on Materials to Cut Costs
One of the most common mistakes people make when installing a concrete pad is trying to save money by cutting corners on materials. While it may seem like a good idea to opt for cheaper concrete or use less material, this can lead to problems down the road. Lower-quality concrete mixes are more prone to cracking and wear, especially in harsh weather conditions. Additionally, using the right amount of concrete is critical for ensuring the pad’s strength and durability, especially if it will bear heavy loads like vehicles or equipment.
To avoid this mistake, always choose high-quality materials and consult with professionals about the correct concrete mix for your project. Spending a little more upfront will save you from costly repairs or even complete reinstallation later on.
Neglecting Site Preparation or Drainage Considerations
Proper site preparation is crucial to the success of any concrete pad installation. Failing to clear and level the site properly can result in uneven surfaces, which may cause cracks or structural weaknesses over time. Without a solid, level foundation, the concrete pad will not be able to withstand the stresses it’s meant to bear, leading to early deterioration.
Another overlooked aspect is drainage. Poor drainage can cause water to pool around or under the pad, leading to erosion and weakening of the concrete. This is especially important in areas prone to heavy rainfall or water runoff. Without adequate drainage, water can seep into the concrete, freeze during colder months, and cause cracks.
Ensure the site is properly leveled and compacted before pouring the concrete. Installing a drainage system around the pad, such as gravel-filled trenches or sloping the pad slightly for water runoff, will help prevent water-related damage.
Failing to Check Permits or Local Regulations
Overlooking the need for permits or failing to comply with local building regulations is a mistake that can lead to serious legal and financial consequences. In many parts of New Zealand, certain structures, including concrete pads, require permits or adherence to specific codes, particularly if the pad is being used as a foundation for a building or driveway.
Skipping this step can result in fines, project delays, or even the need to remove and redo the work to meet legal requirements. Additionally, when selling your property, any unpermitted structures can create problems with the sale.
To avoid this mistake, always check with your local council or governing body to understand the permitting requirements for your project. It’s essential to ensure your concrete pad complies with all building regulations before you begin any work.
Not Allowing Proper Curing Time
A critical, often overlooked step in concrete pad installation is allowing adequate time for the concrete to cure. Concrete doesn’t simply dry; it undergoes a chemical reaction that strengthens it over time. Skipping or rushing this curing process can significantly weaken the pad, making it more prone to cracks and surface damage.
Typically, concrete takes around 24 to 48 hours to set enough to walk on, but it needs a full 28 days to cure completely. During this time, it’s important to avoid placing heavy loads on the surface or exposing it to extreme weather conditions. Failure to allow the concrete to cure properly can result in surface defects, structural issues, and reduced longevity.
To prevent issues with curing, plan your project timeline to allow for the full curing period. Protect the concrete from heavy rain, extreme heat, or cold by covering it with plastic sheeting if necessary. Waiting for the proper curing time will ensure your concrete pad is strong, durable, and long-lasting.
By being mindful of these common mistakes, you’ll increase the chances of your concrete pad being a successful, durable addition to your property. Paying attention to quality materials, proper preparation, and compliance with local regulations will help ensure that your investment stands the test of time.
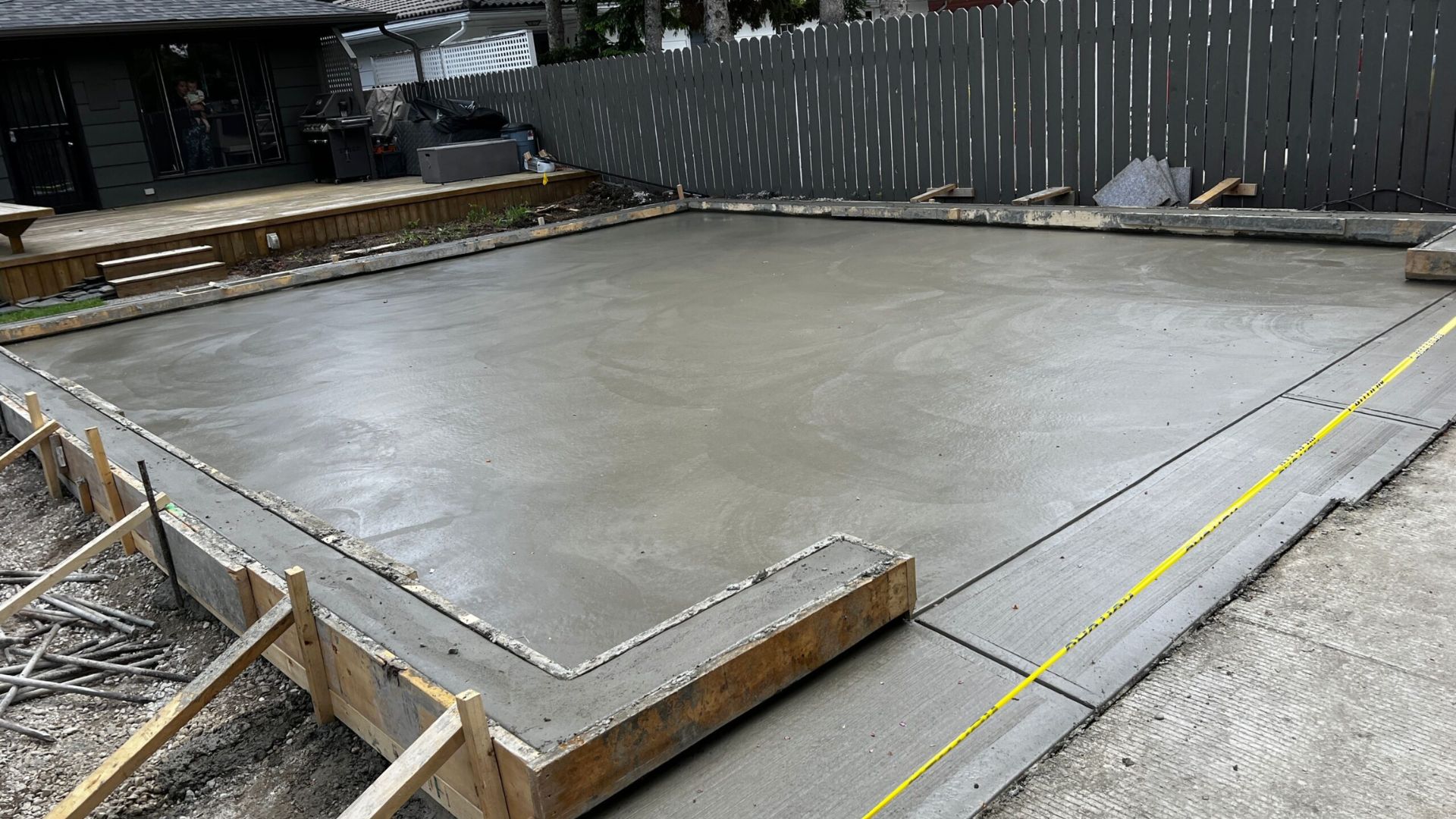
FAQs: About Concrete Pad Cost NZ
Conclusion
In conclusion, understanding the factors that influence concrete pad costs in New Zealand is crucial for making informed decisions about your project. The size of the pad, its thickness, the type of concrete used, labor charges, and site preparation all play significant roles in determining the final cost. It’s important to carefully plan your project, factoring in both immediate and long-term needs, and avoid cutting corners that may lead to costly repairs down the line. Take the time to gather multiple quotes from reputable contractors and weigh the value of quality workmanship over purely price-based decisions. By doing so, you’ll ensure that your concrete pad is durable, reliable, and meets your expectations. For a more tailored estimate based on your specific requirements, consider reaching out to experienced professionals who can provide detailed advice and pricing.
About the Author:
Mike Veail is a recognized digital marketing expert with over 6 years of experience in helping tradespeople and small businesses thrive online. A former quantity surveyor, Mike combines deep industry knowledge with hands-on expertise in SEO and Google Ads. His marketing strategies are tailored to the specific needs of the trades sector, helping businesses increase visibility and generate more leads through proven, ethical methods.
Mike has successfully partnered with numerous companies, establishing a track record of delivering measurable results. His work has been featured across various platforms that showcase his expertise in lead generation and online marketing for the trades sector.
Learn more about Mike's experience and services at https://theleadguy.online or follow him on social media: